製品の品質とコストの80%は設計段階で決まると言われる中、設計力向上を課題として認識されている企業は多いのではないでしょうか?しかしいざ設計部門の改革に着手しようと思っても、どこから手をつけるべきかわからない、他社と比較して自社の設計部門の実力がどの程度か把握できていない、などの理由から設計部門改革への取組みが、なかなか進まないという声を良く耳にします。そのような状況にある設計部門にお勧めしたいのが「設計開発力診断」です。この診断は各企業の設計部門の実力を、一般的に設計の実力が高いと言われる企業と比較して、どういうレーティングになるのかということをご提示し、改革へのロードマップ作成に向けた指標をご提供するものです。
この診断を行う際には①開発プロセス②製品アーキテクチャー③ I Tシステムの活用④人材育成・技術継承という4つの視点で、企業の設計開発力を評価しています。
ここではこの4つの視点について具体的に説明していきたいと思います。
1 開発プロセス
まずフロントローディングについてですが、出図遅れがあった時に、検討開始をもっと前倒しにすればいいのではという、間違った使い方をされている管理職の方をよくお見受けしますが、フロントローディングとは、ある目的達成に向けた手段であり、プロセスの改革です。例えば提案依頼、見積り依頼の営業段階に、設計部門が設計のピークを前倒しして、参画し、御用聞き営業から脱却し、攻めの営業への転換を図るということが、設計のフロントローディングとしてあげられます。今後サプライヤーは提案型でないと生き残れないため、この取組みはさらに重要になると思われます。また、3次元データがあることが前提ですが、出図する前に、性能、生産性、コストダウン案など、色んな評価を前倒しで検討して、出図段階ではその辺の問題を全て消してから出すというようなコンカレントエンジニアリングの取組みも、設計のフロントローディングの一つです。従来の設計業務における、企画段階~基本設計~詳細設計~製造試験という並びが、フロントローディングでは、基本設計、詳細設計は期間も工数も増えるため、設計にかかる負荷は非常に大きくなります。ただこの取組みにより、設計後の試作や試験の期間が短縮され、一番コストの高い部分が減るという効果があります。これらフロントローディングとコンカレントエンジニアリングの取組みにより、1980年から1990年の間に、自動車メーカーでは相当な期間短縮と試作の削減を経験してきました。そしてその先進的な取組みは、自動車部品メーカーやその他大手の製造業にはその5,6年後ぐらいに伝わり、その他業界へは10年後、中小のメーカーなどには20年ほど遅れで伝わったと思われます。中小企業は、自動車メーカーがいろんなことを試した成功例、失敗例から学べば良いのですが、まだ現状で2次元CADを使っている会社が、あと2,3年で3次元に切り替えるような場合には、改善ベースで取組むのではなく、自動車メーカーの事例をあるべき姿として、そこまで一気に飛ぶことが可能です。これには改善ではなく、改革として取組まなければ、そこまでは到達できないという覚悟が必要になると思います。
2 製品アーキテクチャー
モジュールデザインと言う考え方が現在のトレンドで、私のところにも自動車部品メーカーをはじめとして、様々なメーカーから引き合いが来ています。モジュールデザインはニーズの多様化、非常に多くの仕様への短納期対応など、現在の設計部門の負のスパイラルが要因として出てきたものです。モジュールデザインはスウェーデンのスカニアという中堅のトラックメーカーが起源と言われています。特筆すべきはその利益率の高さで、ベンツ、ボルボなどの大手メーカーの利益が5%程度であるのに対して、約20%の利益を出しているのです。そしてその成功要因が、このモジュールデザインにあると言われていて、それを2000年ごろからVW、トヨタなどが追随していったという歴史があります。モジュールデザインは自動車メーカーだけのものではなく、製品設計を行っているメーカーのアーキテクチャーのパラダイムシフトと言われており、個別受注型メーカーも含めて全ての製品開発に適用できます。実際に取組みを進めている自動車メーカーではモジュール化によって投資・コスト及びR&Dへの投資が2割~3割減らすことができたという報告もあります。
3 I Tシステムの活用
2000年に入ってCADの性能が飛躍的に向上し、ハイエンドCADという高価なものを使えば、ベテラン設計者が行っている作業を自動設計で取込めるようになりました。設計作業の6、7割を占めるルーティン作業を機械にやらせるイメージで、それにより出来た時間で設計者にはもっと創造的な仕事をしてもらうことが狙いです。またCAE変遷の流れとしては、設計が2次元から3次元に変わることで、それまでのトラブルシューティング型解析から、バーチャルシミュレーションへの進化により、出図前に品質をシミュレーションできるようになりました。これを活用した設計者CAEが最近のトレンドで、3次元CADの中にCAEを組み込むと、設計者がパラメータを指定することで、性能、コスト、重量情報などが全部出てくるため、設計者自らがCADで設計しながら、どういう構造的な特性になっているかというのを、リアルタイムで見ながら、最適な仕様の検討を行うことができます。すでにそういう最先端の取組みを進めている自動車メーカーもあります。ただここでの注意点は、3次元CADの導入だけでは、効果は非常に限定的だということです。フロントローディング、コンカレントと言ったプロセス改革を同時に組み合わせることではじめて効果が出て来ます。経営者の方は色んな基盤システムの導入を検討されていると思いますが、システムはツールであり、その先の達成したい目的が明確でないままにシステム導入自身が目的となっている場合は、確実に失敗するということをお伝えしたいと思います。
4 人材育成・技術継承
昔の日本の製造業の人材育成はOJTがメインで、先
輩の背中を見て育つということが普通でした。ところが自分が自動車の設計をしていた頃に経験したことですが、アメリカの自動車メーカーと一緒に仕事をした際、アメリカの会社では設計者が途中で交代することがあっても、マニュアルが完全で設計の標準化が確立しているため、業務の引継ぎに何の問題も起こらないということに驚いたことがありました。「IDEF0」というアメリカの国防総
省が開発したシステム化の標準技法は、欧米系ITベンダーでは当たり前にプログラム開発の為の業務プロセスの見える化に活用されていますが、その手法をOJTが崩壊した日本の製造業の設計現場に技術継承・人材育成の観点でプロジェクト導入しています。例えば自動車のドア設計は非常に限られた人間しかできませんが、その設計のノウハウ、暗黙知をこのIDEF0で書き出して、それをITベンダーのCADオペレーター(設計素人)が自動設計を実装できるという実績があります。IDEF0を設計手順として、その中に設計基準などをリンクで貼り付けておくことで、設計手順書をベースとした技術継承が可能となります。
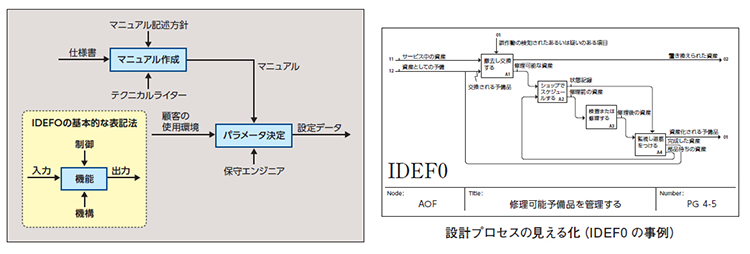
以上、設計開発力診断の評価における4つの視点についてご紹介してきましたが、設計開発力診断の際に、お客様より「最強の設計部門」の定義についてのご質問をいただくことがよく有ります。私の定義としては、ベテラン設計者のモチベーションが高い状態にあること。これがまず一つ目のキーポイントです。そしてもう一つは若手設計者の戦力化です。設計者自らが学んで、自らのスキルを上げていくような組織になればモチベーションは確実に上がって行き、部門全体は底上げされます。そのような状態が実現できれば最強の設計部門となるはずで、そのための第一歩として、ぜひ設計開発力診断の受診をお勧めしたいと思います。