株式会社石井工作研究所は、「たゆまず前進する技術と創意工夫によって社会に貢献する」という創業理念のもと、1974年に大分市に誕生し今年で48年になる。低騒音、省エネルギー、省スペースをコンセプトに、切断・成形・マーキング・製品検査など幅広い工程に対応した装置を提供するとともに、技術革新と業界構造の変化に迅速に対応し、顧客のニーズを的確に把握、開発から設計・製造・組立・販売・サービスまでを行う装置製造メーカーとして高い評価を受けている。
1970~80年代、シリコンアイランドと呼ばれた九州には数多くの半導体工場が集積していた。精密金型を強みとする株式会社石井工作研究所は、大分に進出した大手デバイスメーカーからの要請により半導体製造装置の開発に着手、当時としては革新的なコンパクトで低騒音の電動プレス製造装置を世に送り出し多方面から高い称賛を浴びた。しかしバブル崩壊後、世界的に半導体事業の競争が激化し、再編が加速するとともに、その多くが海外に移行する中、当社は国内の半導体マーケットの縮小を、自動車関連の部品製造装置分野でカバーすることで業績を伸長させてきた。近年では、さらにグループ会社とのシナジーによりIoTやドローン、ロボット事業の領域にも進出し、モノづくりとセンシング技術を融合させた新しいチャレンジを進めている。部門間を越えた連携と意識改革、徹底した見える化で職場の課題を克服してきた曲工場の改善活動を紹介する。
金型製造から半導体製造装置、そしてロボット事業へ
金型から半導体分野に進まれたとのことですが
中村氏: もともと当社は金型メーカーとして、半導体向けの金型や樹脂製品の成形金型などに取り組んで参りましたが、約30 年前に当地に進出されたお客様から依頼を受け設備装置の開発を始めました。
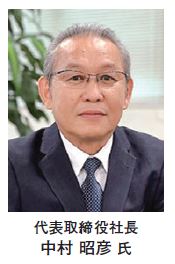
当時はシリコンアイランドという触れ込みで、大分をはじめとする九州地方では半導体産業の誘致がとても盛んでした。その時代はまだ油圧プレスが使われており音が非常に大きく、荷重制御もできておらず、お客様からとても困っているとの声が多く聞かれていました。当社は、そのようなお客様の課題を解決しようと当時では珍しい電動のサーボモータを使ったプレスの開発にチャレンジし、業界で初めてサーボモータを使った電動プレス「ソフトプレス」の商品化に成功することができました。当時は騒音暴露基準が80デシベルという時代でしたので、その基準よりもはるかに低い60,70デシベルという「ソフトプレス」は(当時)大きな反響をいただくこととなり、ヒット商品となりました。
バブル崩壊後、海外勢の技術革新や安い労働力の優位性もあり半導体分野は急速に海外シフトが進みました。当社が行っているのは半導体の後工程ですが、その多くは中国、韓国、台湾、ベトナムなどとの価格競争で海外展開が進みました。当社にとっても急激に国内の引き合いが減少し、大変厳しい時代でした。そこで、新規参入したのが、自動車業界でした。2000年のことです。
当然のことですが、新たなマーケットへの挑戦は当初は大変苦労しました。しかしながら、そこでも「お客様のニーズに応え、たゆまず前進する技術と創意工夫」という当社の姿勢を評価していただき、今では大手自動車部品メーカー様にも「ソフトプレス」をはじめとする数多くの製品を納入させていただいています。
最近の新しい取り組みはありますか
中村氏:
以前は「いいモノを造れば必ず売れる」、特に日本製品は圧倒的に技術的にも優位にあり、少々価格が高くても売れる時代でした。しかし今は違います。世界中にモノがあふれ、海外の技術力も急激に進歩し、日本よりも先行している技術も少なくありません。当然お客様もグローバルな競争の中で生き残りをかけ、生産の高度化を目指して取り組んでいるため、我々は常に「お客様が望むもの」を「お客様の期待を超えるレベル」で提供していく「技術力と知恵と努力」が必要と考えています。
そのような中、現在の当社は2018年に通信インフラを展開するモバイルクリエイト株式会社と経営統合し、いまの新しいFIGグループ体制に変わりました。これからの世の中は、人口減少や高齢化が一段と加速していく中で、今までとは比較にならないレベルであらゆるシーンで効率化が進展していくと考えています。ネットを通じてあらゆるものが繋がり、AIを駆使しながらコントロールしていくまさにSociety5.0の時代です。今当社が特に関心をもって取り組んでいるのは、ロボットの製造です。当社のモノづくりの技術とモバイルクリエイト社の情報通信技術のリアルとバーチャルの融合により、社会やお客様に様々なサービスが提供できると考えており、永年の経験で培ってきた半導体の製造設備、金型、精密加工、自動車関連の部品組付け装置に加え、ロボットという新しい事業の5本柱で成長を目指しているところです。
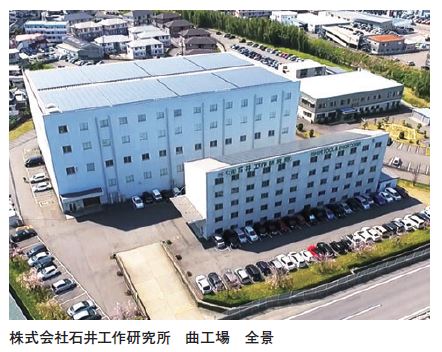
生産性の指標づくりと見える化
活動開始の背景には何がありましたか
中村氏: この活動が始まったのは4年前です。テクノ経営総合研究所様にお願いした背景は、景気の変動や国内の半導体マーケットの縮小から約300名の社員を抱えながら経営を安定させていくには、従来のビジネスモデルでの限界を感じていました。しかし、新たなチャレンジをするためには、片手間ではできず、相応のリソースと投資が必要となります。しかし、現実は足元の仕事で手一杯な状況。何とか現在の人員の中で、既存の事業をしっかり維持・成長させながら、会社に新たな事業にチャレンジできる余力を生み出すためにはどうしたらいいか。そのためには、生産性を上げるしかない。そのような思いでテクノ経営総合研究所様の1日工場診断をお願いすることにしました。
工場診断を受けたご感想はいかがでしょうか
中村氏:
私も入社して40年になりますが、外部の人から当社の生産体制のなかに入って見ていただいたということは、今まで一度もありませんでした。そのため、社風としては閉鎖的な一面があり、新入社員は先輩の仕事をみてそれが良いと思い、疑問をもたず言われたとおりに仕事をしていく。そういう文化だったのです。
1日工場診断の結果報告では、わずか1日見ていただいただけで「御社は50%位しか稼働率が上がっていない」という大変厳しい評価をいただきました。正直ショックでしたね。私も長年この会社にいるので正直「そんなことはないだろう」と心中で思いました。ところがその説明の中で、「各工程に優劣を測るモノサシがない。だから何を基準に良い悪いの判断をしているのかわからない。そこが弱点だ」というのです。実はこのことについては、私自身も常々感じていたことでもありました。ワークサンプリングなどで現場の状況を改めて指摘されると「あっこれだ」と思いました。それでコンサルティングをお願いすることにしました。
全員参加で活動を進める
今年で4年目ということですが、最初はどの部門から始められたのでしょうか
中村氏: 私どもは一貫生産のため、開発から設計、製造、組立まで多くの部門があります。最初は製造部門と技術部門を対象として生産性の指標づくりから始めました。計算式も技術と製造で取れるデータが違いますが、今取れるデータでいかに正しく生産性を表せるかを念頭に置き、3ヵ月くらいかけしっかり議論した上で、全17チームで取り組むこととしました。
そして、一番取り組みやすい製造部門からスタートし、「まずは、見える化」に取り組みました。各製造設備からは稼働率がモニター表示されるようになると、中には8時間のうち4時間くらいしか稼働していない設備があることが表面化し、コンサルタントの中川さんが仰る50%という指摘を徐々に全社員が認識せざるを得ない状況になっていきました。
一つの指標ができたことで、数字にも徹底してこだわり、たとえば以前だと昼休みには全部機械がとまっていたのですが、生産するモノによっては、事前に準備さえしておけば無人運転により生産量は大きくあがる。それからは、昼休みに入る前には1時間で加工が終わるものは機械にかけるように行動が変化し、同様に朝・昼休み・帰りという時間で対応する「おたすけマン」という制度を設けることで大きく意識も行動も変化していきました。
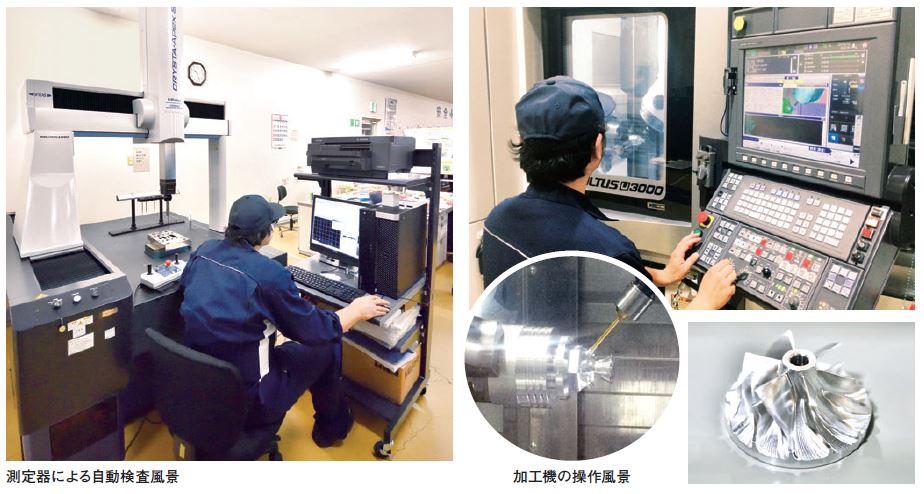
17チームという数はかなりの割合ですね
中村氏: そうですね、前述のように当社にとって、外部の方の指導を受けるのは初めてでしたので、本活動を浸透させていくには「全員で取り組む」ことがとても重要と考えました。当社は、開発・設計・製造・組立・販売・サービスの一貫体制のチームでモノづくりを行う会社です。全社員がこの活動を理解し、意識を変え行動を変えていかなければ会社全体としての効果がでないと考え、ものづくりに関係ある部署はこの活動に参加しています。
現在までの活動についてご説明ください
堀米氏: 1年目は生産性向上の取り組みを通じて主体的に動ける人財育成を進めました。まず改善の仕組みを作っていくことに力を注ぎました。目標は10名分の工数削減でしたが実際には18名分の工数削減を達成することができました。
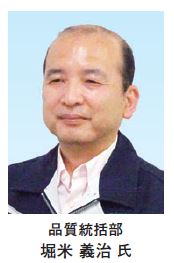
続く2年目は、活動指標をブラッシュアップして、さらに改善のレベルアップを目指し、部門の枠を超えた連携テーマに力点をおいて全体の改善力強化をはかりました。
3年目は売上と収益向上を目標として活人化をテーマに進めました。ちなみに活人化とは人財の有効活用を意味します。
そして4年目の現在取り組んでいるのが、装置をお客様に出荷・引き渡し時に発生している現地の「立ち上げロス」の削減です。これも金額ベースで見える化して提示していますが、無視できないロスです。検査のFMEAによるリスク評価をして、出荷前に問題を全て潰すように取り組んでいます。今後はさらに上流の設計が品質改善に取り組み収益向上に貢献することを目指しています。
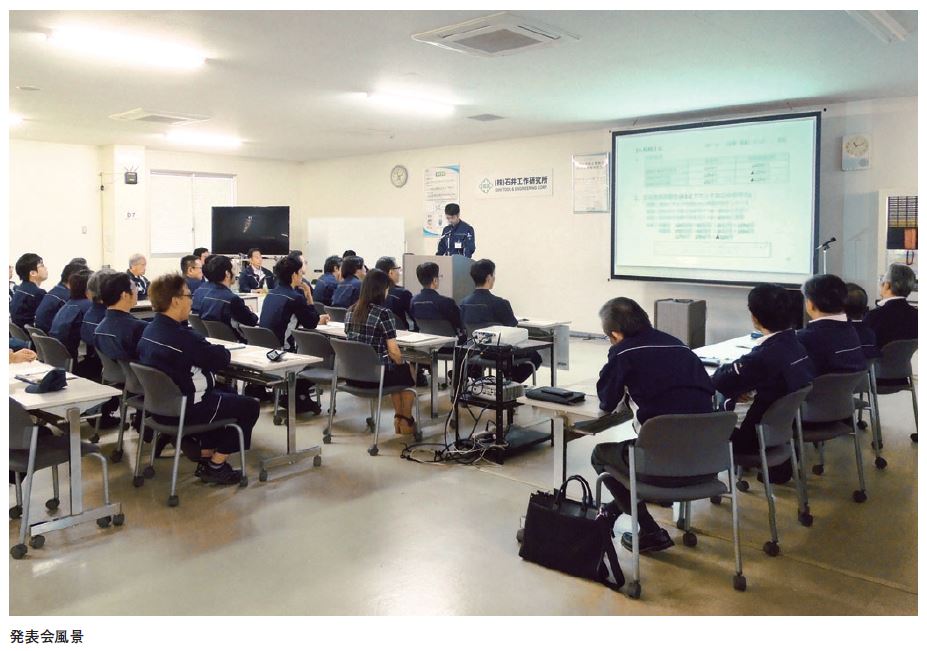
中村氏: 私は朝礼で「製造業の生命線は品質である」と常に伝えています。今までは、ともすると問題が発生してから対策を検討する場合が多かったのですが、そうではなく課題設定型への転換を目指しています。価格競争が一段と厳しくなっていく中、ロスを最小限にすることで納期短縮をはじめお客様の満足度を高め、同時に手戻り防止による収益アップを実現するために、品質保証部門を増員強化し、部に格上げしました。定時開催する「受注検討会」にも品質統括部が入り、過去に発生したトラブルの事例等をあげながら、構想段階で設計者に考えてもらっています。まずお客様に喜んでいただく、信頼関係こそ最高の品質だと考えています。
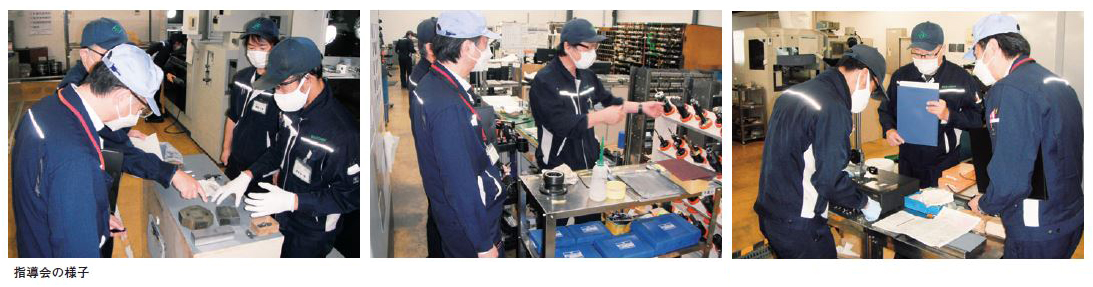
意識改革で生産性が倍増
コンサルティングに対する反応はどうでしたか
中村氏: 繰り返しになりますが、当社は良くも悪くも独自の社風を持っていました。私自身も機械設計の仕事に15年ほど携わっていましたが、新しい発想で図面を出すと「こんなものがつくれるか、お前がつくれ」と製造部門の人から言われたことがあります。そんな風にチャレンジする前に、今までのやり方に対して少しでも変えると非常に反発される。そういう状況が往々にしてありました。コンサルタント導入の感想についてヒアリングはしていませんが、中川さんから伺った内容では指導会の参加率が下がった時期もあったようです。2・6・2の法則ではないですが、どうしても2割位は反発する人が出てくるものです。しかし、そういう社員も全員を対象にした活動を熱心に継続していくことにより、いつしか自分が孤立を嫌がり一緒にやっていくようになるものです。
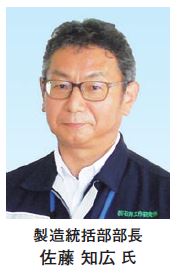
佐藤(知)氏: そうですね。いまだに若干温度差がある部分を感じる時もありますが、社長からの激励もあり、製造部門では意識を高く持って取り組んでくれています。また技術部門も苦労をしながらも確実に力はついていると思います。あきらめず継続した成果、いまでは品質保証の活動を設計にフィードバックしていく動きも始まっていますので、徐々に数字という形で見えてくるようになってくれば技術部門のメンバーのやる気にもさらに弾みがつくと感じています。
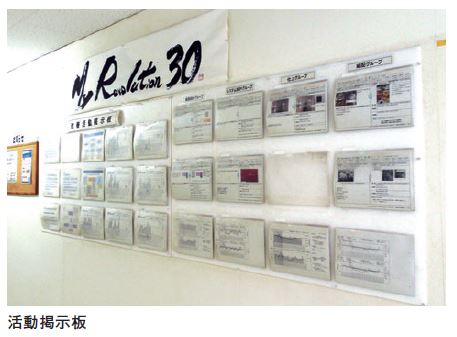
改善活動の成果はいかがでしょうか
中村氏: 究極的には待ち時間をゼロにすること。これは「大きな意識改革」でもあり、だからこそ全員参加でやる必要があったのです。本活動に全員で取り組むことにより、気づく時間というのは比較的早かったと思いますし、結果的には正解だったと思います。月一回の管理職会議があるのですが、他部門との調整についても、「2日くらいだったらうちがバックアップするよ」などの声がでるようになった。「だったらいいよ、日曜日俺がでるよ」という人もいます。この様に意識が変わり、社員と社員が手をつないで協力する体制がとれるようになりました。これは非常に大きな成果だなと思っていますし、業績にも表れています。これも社員の皆さんの努力のおかげです。業績が伸長すれば、少しでも社員に還元していきたい。できれば社員にいまの倍の賞与にしたい。そういう思いで活動に取り組んできました。その結果、製造部門では非常に効率が上がり、活動開始時と比べて生産性が倍増しています。
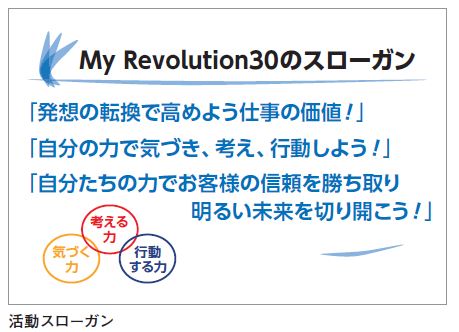
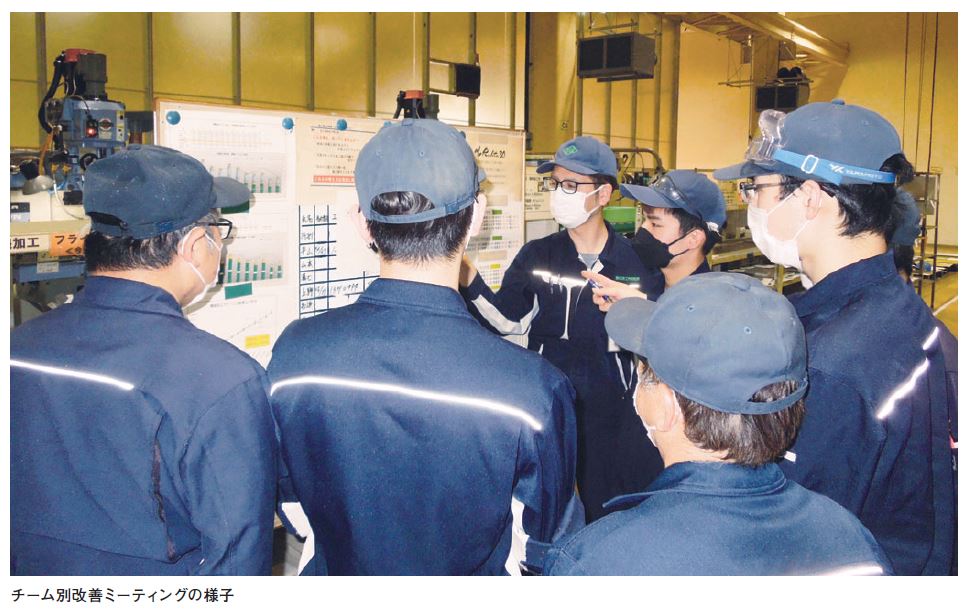
さらなる挑戦に向けて
今後の課題についてお聞きします
中村氏:
現在の課題は、設計など頭のなかでやる仕事の進捗をリアルに見える化することが難しいということ。そのテコ入れをどうするかで対策を練っています。
私がいう見える化というのは、ただ見えるというだけでなく、目指しているのは、今まで興味をもたず見てくれなかった社員が見るようになること。それで、敢えて社内の目につく場所にいろんなものを貼りました。当初は自分ひとりでやり始めましたが、1年たち2年たつと気が付かないうちに当たり前に工場内がそうなっています。
活動当初は製造部門の中でもあれこれと意見を言ってくる社員がいたようですが、今はこの活動に不平・不満を言う人はいません。それくらい変わっています。見えるということの効果です。不平を言う人ってけっこう勝気なんですよね。やる気はあるんですが職人なのです。今となっては新入社員のいい先生になっています。
今後のビジョンについては人財の強化を目指していきます。毎年10名ほどコンスタントに入社してくる社員を一人ひとり大事に育てて、若い力で改善とチャレンジを継続していくことでお客様に必要とされ、外部環境の変化にも耐えられるサスティナブル企業を目指していきたいと考えています。
本日はありがとうございました
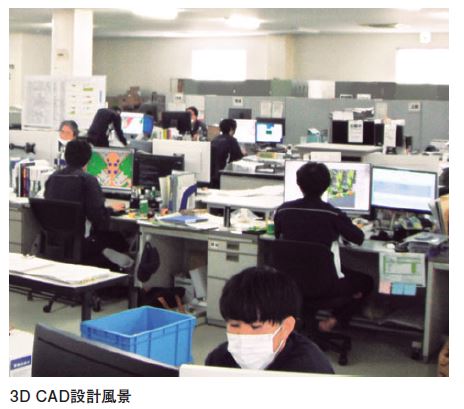
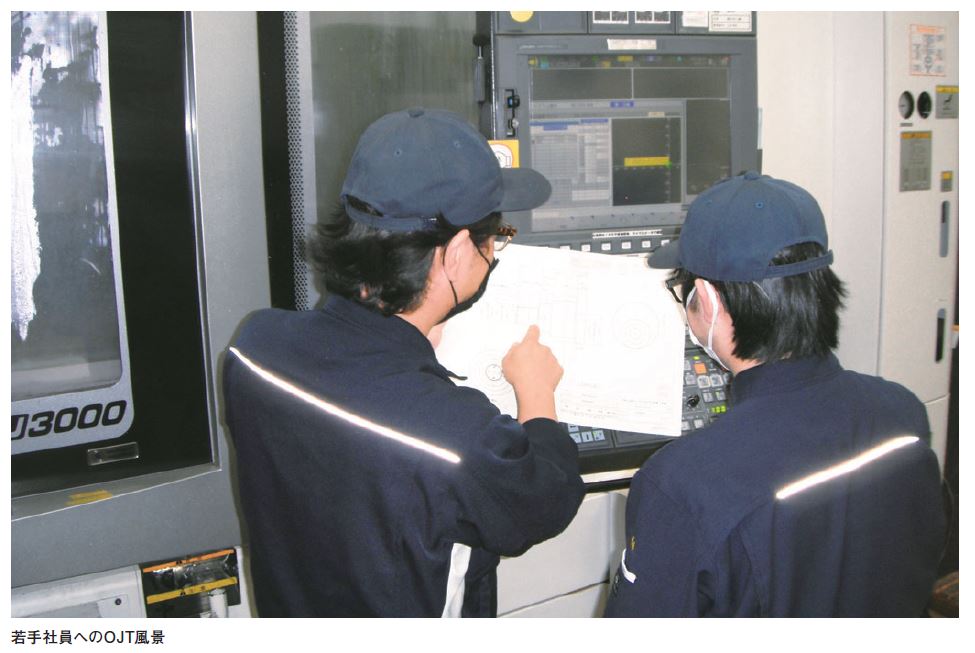
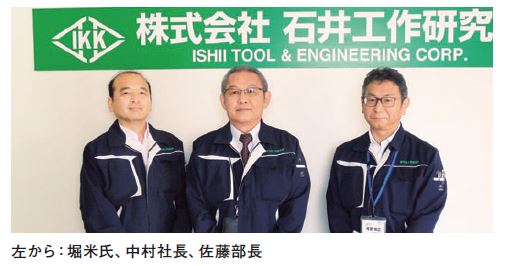
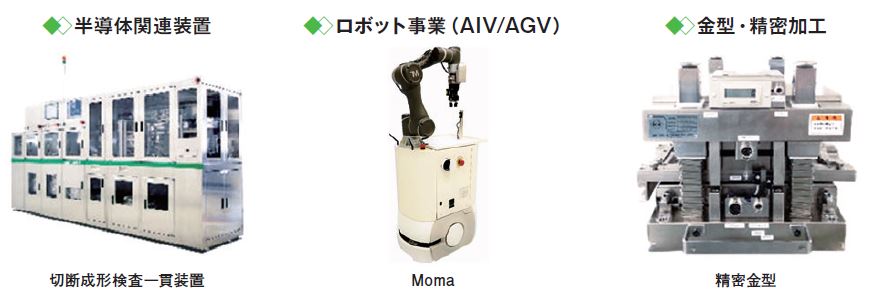
取材にご協力いただいた方
株式会社 石井工作研究所
ISHII TOOL & ENGINEERING CORPORATION
代表取締役社長 中村 昭彦 氏
製造統括部部長 佐藤 知広 氏
品質統括部 堀米 義治 氏
PDFダウンロード
【コンサルティング事例】 株式会社石井工作研究所様