本ページでは、オオサキメディカル株式会社様に対するコンサルティング実績をご紹介しています。
オオサキメディカル株式会社は名古屋市において医療関係材料の製造販売を行う有力企業である。昭和11年の創業以来、70年以上にわたり医療の 現状と真摯な姿勢で向き合い、時代のニーズに応じた商品開発を追求している。最新の製造・試験設備を導入、厳しい品質管理のもとで生み出される 製品は、国内外において高い信頼性を持つ。特に主力の産科・婦人科製品においては、国内シェアNo.1を誇り、海外市場においては中国やインドネシアに 事業展開。現地の医療機関からも高い評価を受けている。
改善活動では、2006年11月より郡上工場の活動を開始、2009年6月からは新工場である岩倉工場も含めて、活動を継続中である。コンサルティングの有効活用で独自の視点をお持ちの大崎社長にお話を伺った。
(※ASAP 2010年 No.3より抜粋)
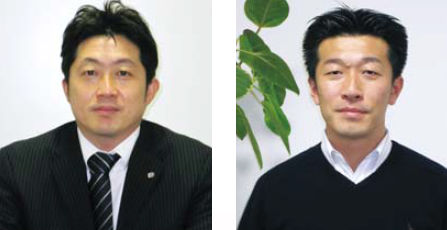
左から代表取締役社長:大崎氏
生産本部 岩倉工場 工場長:船戸氏
最初にコンサルティングを導入された経緯をお聴かせください。
もともと当社はマーケット主体で営業とか企画開発とか、そういうものに力点を置いた経営を約70年続けてきました。 今までの経営の中で営業力や企画力は高い評価をいただいていますが、生産力については今ひとつというのが現状でした。それで、私が生産本部を 統括する立場になったときに改善活動の必要性を感じました。ところが、当時は常務という立場で、営業・システム・人事・経理・生産と全部トップを 兼務していましたので、私がやりたいと思う改善活動を根付かせるための時間が足りません。そこでコンサルティングという形で思想の徹底をはかりたいと 考えたことがきっかけです。
私自身、ビジネススクールでの経験を持っていますのでコンサルティングは身近に感じることができる世界です。周囲でも同期の人達がコンサルタント として活躍しており、その長所や短所もある程度は理解しているつもりです。だからコンサルティングのプラスの部分を有効に活用して活動を進めたいと思いました。
また、物事を変えるためには社内で行うよりも、外部の要素を入れたほうが心情的に社内も変わりやすい。こうした二つの要因があってコンサルティングを 導入することにしたわけです。
コンサルティング活用のために導入時に取り組まれたことは何ですか。
最初は、郡上工場での改善から着手しましたが、当初は活動スタンスについてのすり合わせに時間をかけました。これは、私がコンサルティング嫌いである負の部分 でもあるのですが、コンサルティング会社には各々流儀のようなものがあって、テクノ経営ならVPMにはC改善があってD改善があるというように、どうしても型通りに 進めたいという思いがあるのですね。しかし、私は「型にはめて本当によくなるのですか」「そんなやり方では、誰もついてこないですよ」という問いかけを通じて、 コンサルタントに改善に対する私自身のリアルな思いをどんどん伝えていきました。
活動が始まっても、コンサルタントがしゃべった内容を「こういうことをやらなければいけない」という形で私が説明しフォローする状態が続いていました。活動中は、 実際に私が話しているのが半分以上、それが活動初期の印象ですね。
そうした調整を経て、コンサルタントとの意識も共有されてきましたので、それ以降は 船戸工場長を中心に活動を進め、私も週1回は工場に行って活動をチェックするようになりました。1年目の活動成果としては、みんなの仕事に対する考え方が変わってきたこと。 その要因は実際に改善が目に見える形で実感できたことにあると思います。
その後の活動はどのように進められましたか。
その後、会社買収に関する業務やインドネシアにある子会社の社長も兼任することになり、私も改善にかけている時間がなくなってきました。 そこで、それ以降は現場主導に任せ、動きを見ているのが現況です。
2年目は残念ながら目標達成までには至らず、3年目は、この岩倉工場でも改善活動を開始しました。 当工場は昨年、本社工場を移設した新しい工場です。今回も活動開始時には私が介入しましたが、時間が取れないのでその後はコンサルタントにお願いしている状況です。
今までの活動で全体的に実力がついてきていることもあり、どんどん、きれいなレイアウトに変わってきている。コンサルタント自身も「えらくきれいになっていますね」と 驚いている。みんな要領がわかったせいか、どんどん現場を変えていっています。
今までの活動を通じて変わってきた成果というものは何でしょうか。
活動成果という点では、みんなが生き生きして改善発表会にも前向きに取り組むようになったという事実があります。それはやはり活動を継続した結果ですね。 現場を変えると自分たちも良くなる、また楽になるという気づきが生まれたことです。人というものは変化に対する抵抗が元来強いものですが、それを 「変わったほうが良くなるんだな」と思えたということです。そうすると、「じゃあもっと変えよう」という気になるものです。そういう気持ちの変化は間違いなく 成功談といえます。
ただ問題は、そこから先これを継続してゆく、1年2年という話ではなくて、5年10年続けていくためにはどうしたらいいかといいうことです。 アイデアレベルだけだと「もうやることなくなってきました」ということが必ずでてきます。そこからの変化をどのようにしたらいいか。それが今後の課題です。
今後の活動の方向性についてはいかがですか。
今後の課題に対しては、生産部門として必要なマネジメントの体系を含めた人材育成を主眼として進めたいと思います。品質改善とか生産改善のためにはさまざまな 手法とかテクニックがあります。生産工程でいえばIEというやり方があるし、品質管理であればQC7つ道具といった手法があります。
例えば、品質問題に対する改善アプローチで具体例を挙げれば、当社製品に滅菌パックをした製品がありますが、そうした製品に求められることは、安定的なシール 強度を保ちながら開封時にも破れないということです。つまりイージーピールであって、かつ滅菌性を保証するためにピンホールがないシーリングをする必要があるわけです。 そのときにシールというものは温度と時間と圧力で管理しなければいけないのですが、それにはどういう管理方法がいいのかを考えるためにも、こうした手法や知識を 現場に根付かせることが必要だと思います。

管理手法の定着が必要ということですね。
現状では、まだこうした管理手法が充分に使える状態にはなっていません。だから「グラフの使い方はこういうときに役立ちますよ」とか、「こういうもので 品質管理をしていったらどうですか」いうことをお勉強形式ではなく、実際の事例をもとに改善を通じて教育することが必要です。改善活動も同じことの繰り返しでは マンネリ化してしまいます。活動の理論武装のためには知的刺激が必要だと思います。
現状では、IEといわれても何も語れないと思う。郡上工場を立ち上げた1年目、2年目の世界ではなくて、もう一歩上を目指して、改善ツールの使い方を定着させたい。 現場からの声「こういうことで悩んでいます。どうしましょう」ということに対して「なるほど。そうやってやればいいんですね」「そういうときにこれが役立つんですね」 といった示唆を与える指導を期待しています。
最後に5年後10年後に向けての活動ビジョンをお聴かせください。
気持ちは変わった。しかし「わからないところがある。どうしましょう」が今の状況。当社はトヨタではないから改善や品質管理に対して深い知識があるわけではありません。 だけど、今それで満足してはいないし、もっと変わらなければいけないという思いがあります。
まだ道は3合目ぐらい。これからが品質のクレーム改善と同じで指数的に 難しくなると思います。今まではザルで掬えるほど改善するところは一杯ありました。しかし、これからは、外部から見ても「すごいね」と評価されることを目指して活動を進めていきたいと思います。
本日はありがとうございました。
取材を終えて・・
今回の取材では、コンサルティングを推進する我々としても学ば せていただくところが非常に多かった。若き大崎社長自らが改善の陣頭指揮を執られる姿勢を拝見し、 その熱い思いを感じさせていただいた。コンサルタントはあくまでも活動のサポートをする立場、型にはめるのではなく、経営者の方々の思いを具現化する支援こそ コンサルタントの使命なのだと再認識した次第である。
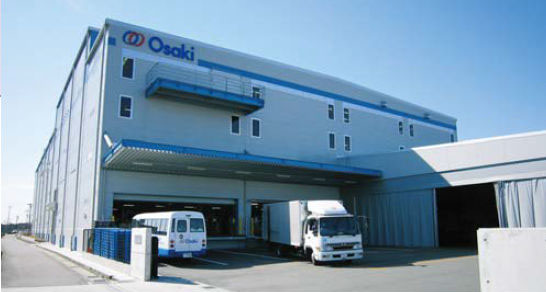
オオサキメディカル株式会社 岩倉工場様様