本ページでは、鉄道リネンサービス株式会社様に対するコンサルティング実績をご紹介しています。
昭和39年(1964年)国際的なスポーツの祭典である東京オリンピックが華々しく 開催された。国内インフラ整備が急ピッチで進み、東海道新幹線が開通した同じ年、 鉄道リネンサービス株式会社は創業した。
鉄道リネンの名はもともと国鉄(現・JR旅客鉄道)の仕事が主だったことによる。 日本の高度成長と足並みを揃えて発展を遂げながら、快適なアメニティ環境の創造を 使命にタオルやシーツ、ユニフォームなどのリネンサービス事業を展開してきた。
近年、列車の高速化により寝台車等のニーズも大幅に減少した。それで現在では、 寝台車に替り、新幹線やホテル、レストラン、病院などの顧客が主流になっているという。
円安による外国人観光客の増加、そして2020年・東京オリンピックに向けて、世界から注目を浴びる “おもてなしの心”。それを支える日本企業として同社の存在は大きい。5年目に入ったという若手リー ダーを中心とするPDCA活動を取材した。
(※ASAP 2015年 No.3より抜粋)
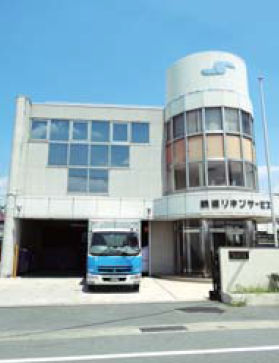
鉄道リネンサービス株式会社様
活動開始の背景
活動を始められた背景についてお話しください
樫根: 当社では、別会社の日本エアリネン㈱と合わせ て、向日町、伏見、高島、西宮、堺の5工場が稼働し ています。そのうち3工場は、シーツ、客室用品など いわゆる「平もの」を扱っており、2工場はユニフォームや細かな製品、顧客支給の品を担当しています。
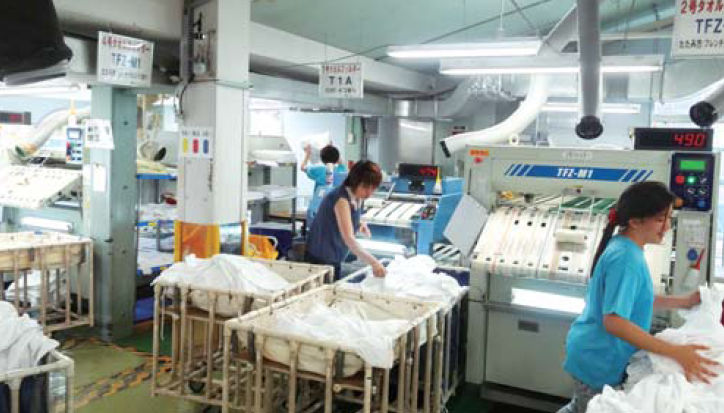
パートさんを中心に業務をこなしてきた当社の特色は女性が多いことです。そのため工場を各地域に分散 させながら働く人材を確保してきました。ところが当業界ではバブル期の頃より深刻な労働力不足に陥りま した。たたみ機、投入機など、リネン業界の機械化が進展したのも同時期で、向日町工場でも過去15年ほ どで30%強の人員が機械化により削減されています。
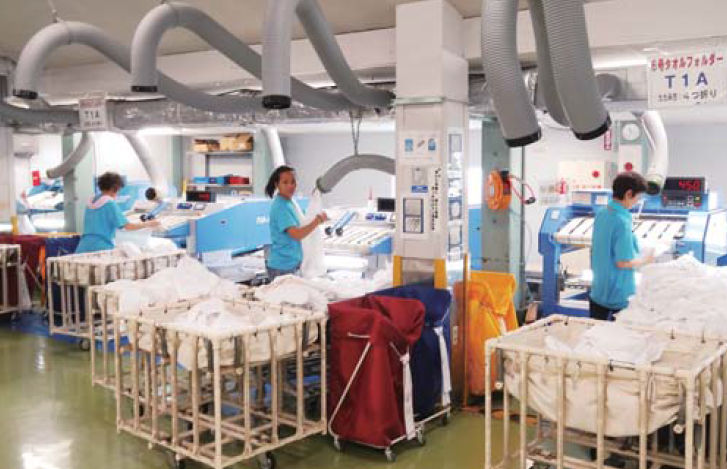
このように熟練を要する工程も機械化で緩和されてきたのですが、アイロンがけなど機械化できない部分 もあります。仕事量が増えるほど人手不足の影響が大きい職場ですので、単独工場では効率が悪く、拠点を分散させながら手間取る仕事は別工場に移管する等の工夫をしてきました。
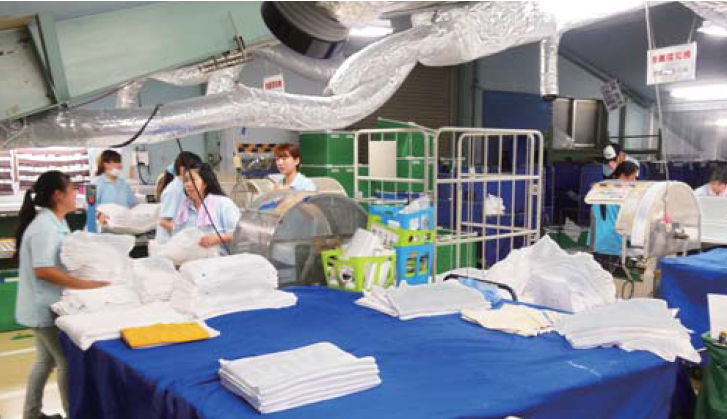
生産性向上のための体制構築については10年ほど前から取り組んできましたが、今回の活動では、若手リーダー育成により競争に打ち勝つ組織作りを進めることにしました。過去にもセミナーや研修会などに社 員を参加させていましたが、コンサルティングを導入して全社展開をするのは初の試みでした。各工場や職 場単位で切磋琢磨し、能力アップする場をつくる。知識として習うのではなく、実践を通じて成長できる活動にした いと思いました。活動は今年で5年目に入りましたが、リーダー育成の成果が現れてきたと感じています。
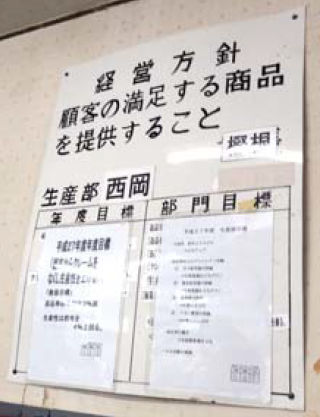
最初の活動はどのように始められたのでしょうか
樫根:
1年目(2005年)は、向日町・西宮工場を対 象に活動を開始しました。両工場を同時スタートさせたのはお互いに競わせる意図からです。結果的にもそ れが正解だったと感じています。
最初はモデル職場として、仕上げ工程である「タオル場」に各工場にそれぞれ1グループを設けました。当 初は午前と午後の半日ずつ栗岡先生(コンサルタント)に京都と兵庫を移動しながら指導していただきました。
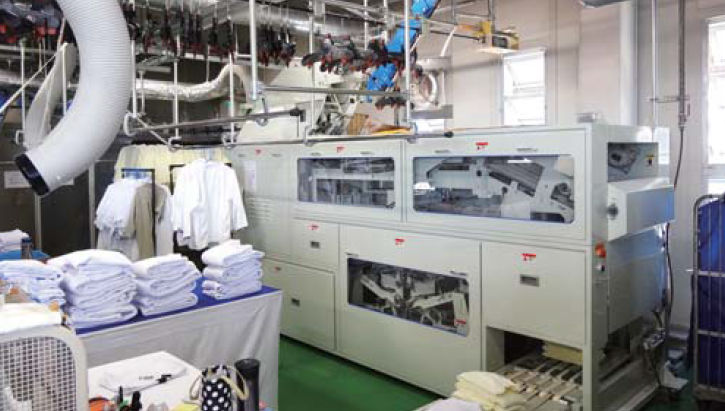
PDCA活動という名称の意味は何でしょうか
樫根: どんな活動もPDCAに沿って進めることが基本 ではないでしょうか。それを継続しなければ現場は良くなりません。当社のように日々同じ作業を続けてい ると、新しいことを考える発想力がどうしても弱くなりがちです。まず自分たちでPDCAのP(Plan)を考え る力を付ける。トップからフォロワーまで、自律性が必要であると感じました。やらなければということは 理解できても、何をどうやるかが難しい。リーダーあるいはマネジメントする立場の人が進んで率先垂範で きるように変わっていく必要がある。そういう意味をPDCA活動は持っています。
活動目標についてお伺いします
樫根:
当社では、人時生産性(1人・時間当たりの生産性)向上を目標としてきましたので、全社活動でも、それを定量目標として踏襲しました。そして目標達成 に向けた意識改革が定性目標です。
当社の工場は日曜が休みなので、土曜日に週単位の仕上げ数を集計して生産性を見ています。
現在ではデータ蓄積により大勢は読める状況になりましたが、たとえばホテルの場合、宿泊数や 使用枚数が事前に把握できず、顧客から戻ってくる量か予測できないリスクがあります。
また汚れの程度や痛み具合も様々です。また繁忙期と閑散期では生産性も大きく変動しますので、それを いかに読み込んで平準化していくかが重要です。こうした改善を進めていこうと思いました。
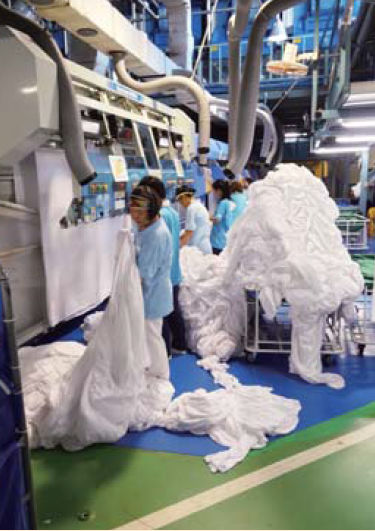
リーダー育成の対象はどんな方ですか
樫根:
入社2~3年目の社員をリーダーに抜擢してい ます。従来なら班長や係長などがリーダーになる場合が多いのですが、当社では世代交代のために若手にも っと勉強させたいと考えています。
チームの人員は、多いところで15名、少ないところで5名位ですが、相対的にメンバーの年齢が高く、 パートさんで勤続30年という人も大勢います。平均的な勤続年数は18年位ではないでしょうか。
彼女たちには長年やってきた自分独自の方法があり、経験の浅いパートさんも発言力の強い古参のやり方に 習ってきました。しかし、それでは改善の余地がなく、ずっと同じことの繰り返しです。そこで入って2~3 年の社員にリーダーになってもらい、作業を見直してみることにしました。
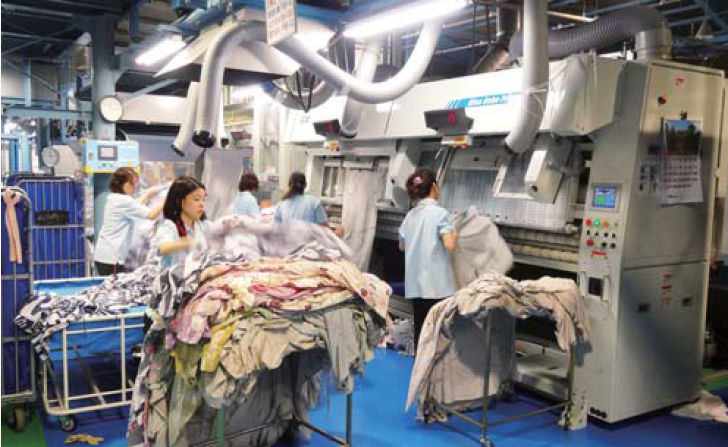
若手とベテラン間に軋轢はないのでしょうか
樫根: 逆に何もわからないから良いのではないでしょうか。リーダーの役割は皆さんに自分たちの問題を出してもらうよう促すことですが、ベテランのパートさんも自分 の子供以下に教える感覚なのでしょう。「こうやっていたけど、この方がいいのとちがう」といった感じで、「それ じゃ一回やってみようか」と改善に取り組んでいます。それでもアドバイスが不足する場合は、専任さん(活動 事務局)や工場長が各チームをフォローアップしています。
活動成果―身についてきた問題発見力
改善活動を通じて変化したことは何でしょうか
樫根:
まずメンバーたちの意識が変わってきました。 当社の場合、工場には「洗濯」「仕上げ」「出荷」の3工程しかありません。ですから技術的な問題より工程間 の引継ぎやコミュニケーションが重要なのです。
従来は、ただ単に「洗濯」から「仕上げ」に品物を渡すだけでしたが、作業しづらい場合の注意点、汚れの 多さなどを伝達するコニュニケーションが見られるようになりました。
たとえばサイズの共通化なども生産性に結び付いてきます。できるだけ品種を少なくしなければ切り替え ロスの連続になってしまいます。今までは口頭だった内容もメモで伝えることで、情報の蓄積や振り返りが できるようになりました。
また5Sについても、以前は場当たり的に行っていた感がありましたが、今ではモノの置き場ひとつにし ろ、いろいろ考える習慣が付きました。ここに置いたら便利、良く出るものはここにおきましょう、あまり 出ないものは倉庫に入れようとか、そういった発言が見られるようになりました。
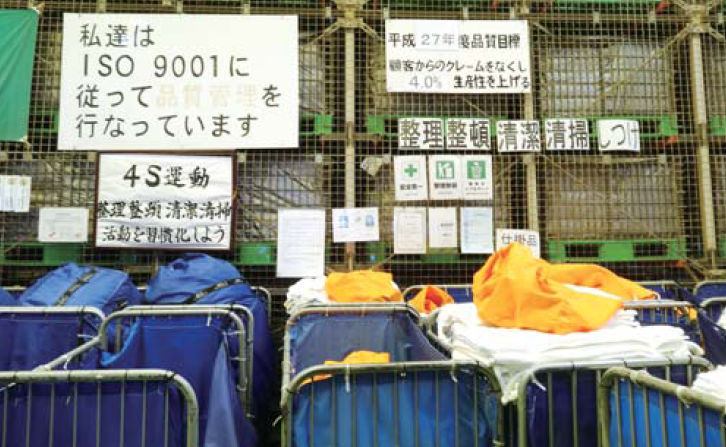
生産性アップの観点ではどうでしょうか
樫根:
生産性については、以前から1日当たり何枚と いう目標はありましたが、バラツキが非常に多く発生していました。一般の製造現場なら10%も20%も バラつくことはないと思いますが、当社では10%程度のバラツキは日常的で、ひどいときは20%くらい に達していました。
たとえば1日1人100点のノルマなら、80点しかできなかった翌日には110点に上がっている。こん なバラツキがあったわけで、それをなんとか平均化しないと品質も安定せず、仕上がり可能な枚数も予想で きません。
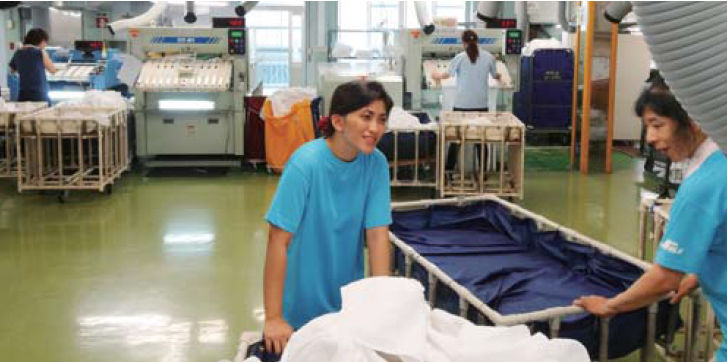
そこで活動のなかで、なぜそんなにバラつくのか。今日は何が悪かったのか。そうした原因を活動により 見つけ出そうとしてきました。その結果、いまでもバラつきはありますが、月別にあった大きなバラつきも 徐々に平均化し5%以内の精度に抑えられるようになりました。
栗岡:
問題の原因探索に4M(人・材料・機械・方法) の視点があります。この4つに問題があるかどうか、それを見ることで改善の眼を養うことができます。どんな目線で改善すればよいか。その切り口をこの4Mが与えてくれます。各テーマに潜む問題を発見・展開 していく。これが問題解決のストーリーとして有効な方法だと思います。
職場にはベテランもいれば若手もいて、手の速い人もいれば遅い人もおられます。そうした作業をどうす れば均一化できるか。また機械にも調子の良し悪しがあり、そうしたバラツキをどう解消するかが課題です。 たとえば材料の捉え方。材料とはシーツとかタオルなどではなく、前工程も材料に含めて考える発想。「仕上 げ」の前工程は「洗濯」ですが、その間の連携が曖昧だとうまくモノが流れない。 だから前工程も材料だという視点で一番良い方法を自分たちで考えていこう。そういった着眼点を持っていただいています。
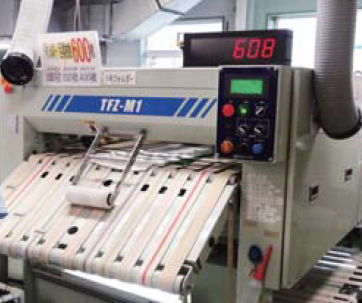
PDCA活動の発展
他工場を含めた活動はいかがでしょうか
樫根: 当社では年2回の活動発表会を開催しています。 発表会は自分たちの日頃の成果を報告する場です。発表者はリーダーですが、他の工場からも参加していますので、非常に刺激になり、お互いの競争意識に火がつきます。
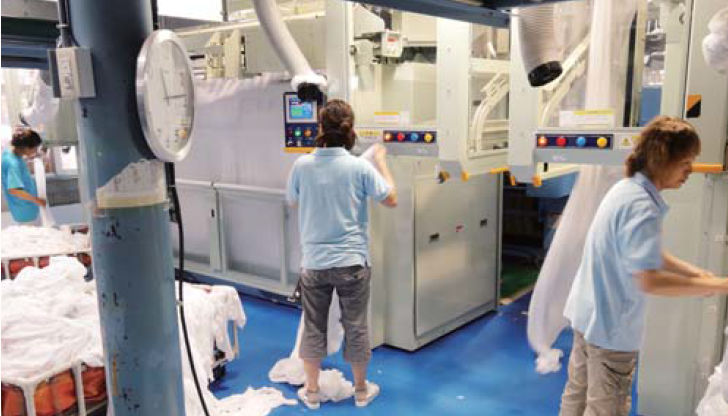
3年間の成功事例を水平展開させて、現在では伏見工場と堺工場でも活動を推進しています。伏見は約50 名、堺が40名程度で同様の活動をしています。つまり4工場が切磋琢磨する場が発表会で、活動を始める 前から、発表会を見学していた伏見工場は活動開始一年で一挙に生産性が上がりました。
発表会では管理職が採点して、優秀なチームを表彰するのですが、みんな楽しんでやっていますね。発表 や資料作りもずいぶん上手になったなと感じます。
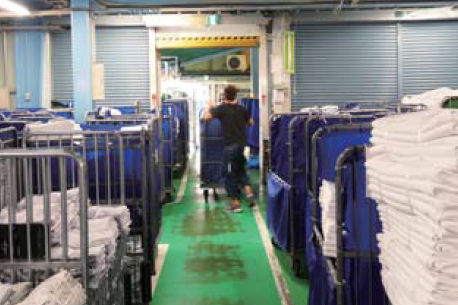
今後の活動の課題は何でしょう
樫根: 課題は山ほどあるのですが、やはり生産性を高 める活動を進めるなかで新しいリーダーを発見していくことが大切だと思います。新しい人に未経験の仕事 をしてもらい、いままでやってきた人がまた別の仕事をやる。社員が常に新しいことにチャレンジしながら 成長して行ってほしいと思います。
ありがとうございました。
【実践事例編】西宮工場におけるPDCA活動 日本エアリネン株式会社 西宮工場様
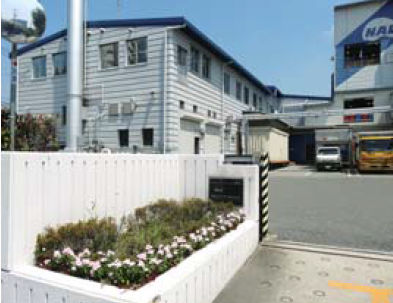
日本エアリネン株式会社 西宮工場様
西宮工場では、約100名の社員・パートを中心にしてPDCA活動を進めて います。現在、事務局の専任2名と私で全体のフォローを担当しており、全 体ミーティング時には最低2名は参加するようにしています。当工場でも、経験の浅い若手社員がリーダー を担当していますが、ベテランを含めてチームを引っ張っていかねばならず、なかなか難しい点もあります。 全員が自分より年上の方なので、言いくるめられる場合もしばしばです。ただ間に 入ってくれる人もいて助かっているようです。当工場の改善事例のいくつかを紹介したいと思います。
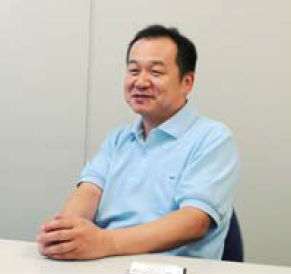
西宮工場 仲野工場長
「C改善シート」提出率100%
現在、西宮工場では7チームほどに分かれて改善活動と取り組んでいますが、活動は生産性向上を前提に 自分たちで進めているC改善(日常改善)が中心になります。各人が気づいた問題を「C改善シート」に記 入して提出するものです。目標件数は、活動開始時には1週間に2枚というハイペースでしたが、今は1か 月に2件としています。それでも提出率は100%をキープしており、現在までの通算の提出件数は12,753 件に達しました。またこの問題に対する解決率は89%でした。
またD改善(プロジェクト型改善)は、全社的に自分たちが取り組むべきテーマを掲げてもらっています。 毎年、半年間でそれを成功させることを目指してきました。
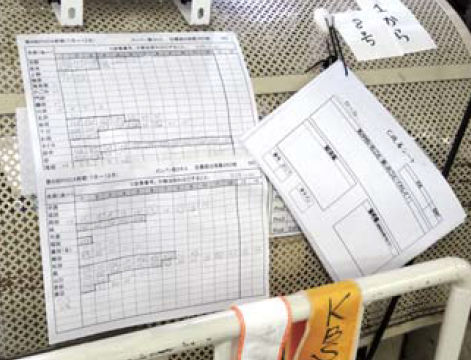
C改善シートと集計表
週報提出で進捗チェック
各工場の動きを全体の活動にするために、改善の進捗に関する週報を各リーダーから提出してもらってい ます。繁忙期もあるので、提出の期限は木曜日までとしていますが、ほとんどのグループが火曜日までに出 してきます。週報には私と専任を含め、コメントを書くようにしています。どんな問題が出て何件くらい解決し たか、生産性はどうか。その報告に対してコメントを入れます。たとえば問題の原因追究が曖昧な場合は 具体的な対策をもう一度書いていただきます。こうしたやり取りのなかで、改善の成果を見守っていること がわかる。そうしたことが大事ではないかと思います。
OJTを活性する「教育手帳」
新人教育に関してはマニュアルを作成して理解してもらうようにしました。特に「教育手帳」は、作業を 教えたものが必ず日付とサインを記入するもので、メンバーの現状レベルが把握できるためOJTに非常に 役立っています。
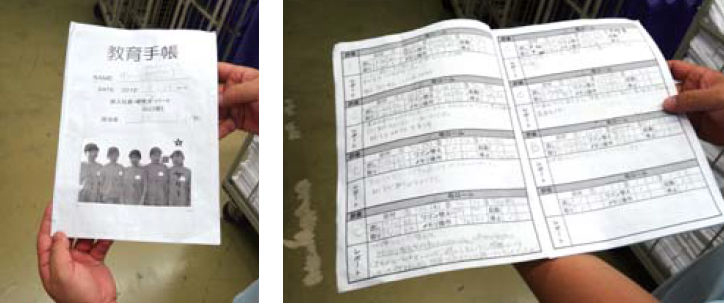
5S活動の定着
当社の工場は、どれだけ掃除してもホコリがすごい職場です。以前であれば、帰るときに少し掃除して終 わりだったのですが、今では始業・終業時にきちっと清掃するようになりました。また週1回は全体掃除の 時間を取って、徹底して工場美化に努めています。また整理・整頓という点でも職場がずいぶんきれいにな りました。
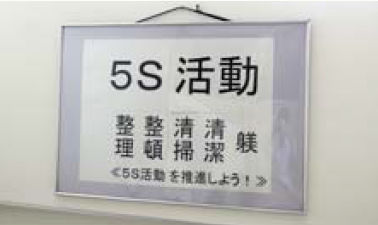
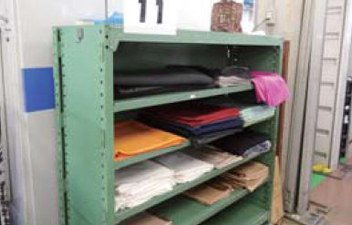

出荷の際、外部から侵入した野良猫がシーツワゴンに乗って足跡が付く、ときに放尿される場合もありま した。対策として、約600台のワゴンに前掛けとカバーを付けることにしました。前掛けを付けることに より、製品の落下防止に役立っていることもプラスです。モノを汚さないように、カバーが汚れていたら替 えてもらうようにしています。こうした地道な作業も5Sの一つとしてやっています。

ワゴンに顧客先情報を略号で表示しました。以前は表示が消えてしまった、わかりにくいと う声があり、発注書をカートに張り付けることでわかりやすくしました。また、出荷先の地域 別に荷積み場を色別しました。