バスダクトは大電流電力幹線として、コンパクトな形状、電力ロスを最小限にできる、リサイクル率が高い等の理由で、従来のケーブル配電システムに変わって、近年大規模プロジェクト等で使用されるほか、大電流を流す必要がある「変圧器二次側の主幹線」にも用いられる電力用幹線である。銅やアルミニウムの帯状導体を絶縁物で被覆するか、絶縁物で支持し、鉄あるいはアルミニウム板で製作された箱状のケースに納めたもので、電磁波の発生が低く、人にもコンピューター回路にも影響の少ないクリーンな幹線である。さらに取り外した幹線は、ケース、導体、絶縁物をそれぞれにリサイクルできる資源再利用型であり、人と地球に優しい部材であることから、近年建設現場での採用が増加している。このバスダクトシステムを創業当時から50年以上作り続ける国内で唯一の専門メーカーが共同カイテック株式会社だ。国内外23,000件を超えるバスダクトの納入実績を持つ同社では、バスダクトの需要増加に対して、これまでの製造拠点である「神奈川技術センター」の老朽化に対応して、バスダクトの安定供給とBCP対策などへの対応の観点から新たな製造拠点「綾瀬プラント」の建設を2020年春の竣工を目指して進める事になったが、その中で、新工場立上げの知見やノウハウが社内に不足していることがプロジェクトメンバーの頭を悩ます大きな要因となっていた。いかにして短期間で既存工場と共に将来のバスダクト事業を牽引していくことができる新工場の立上げを実現するのか?新工場立上げに伴う同社の改善活動について、神奈川技術センター 執行役員 センター長上之門祐一氏、企画開発課 課長 鈴木康之氏、製造部 製造技術課 課長 島田裕士氏からお話を伺った。
創業の経緯、メインであるバスダクト事業の概要についてお聞かせください
上之門氏: 当社では創業当時、電線管と付属部品の代理販売を行っていました。付属部品は多くの種類が各得意分野を持った中小メーカーにより製造されており、当社は各メーカーから仕入れ、品揃えをして販売を行っていたとのことです。
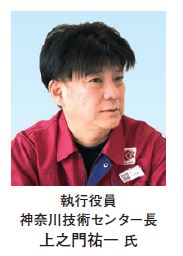
その後昭和31年(1956年)に東京都葛飾区の四ツ木に小規模の工場を設立し、自社製品の製造、販売を開始しました。事業展開としては電線管販売と付属品の販売から徐々に電路資材に業容を拡大する中、お客様からの色々な要望を聞きながら、電線のケーシングとして現在のメイン事業であるバスダクトの着目に至ったようです。そして創業者の友人で日本での電設技術の権威であった某電気会社社長様や某設計事務所所長様のアドバイスを頂き、またそのころ購読していた米国の電設雑誌の記事や広告などでバスダクトの情報を収集し、開発を決意したようです。当時当社が開発したバスダクトは裸導体の各相を隔離絶縁した、いわゆる空気絶縁バスダクト(A-B型)で、日本におけるバスダクトの参入としては4番目の実績だったと聞いています。その後、三菱電機、松下電器(現パナソニック)、住友電工以下電線メーカー6社ほどの参入がありましたが、手間のかかるこの事業から大手企業はどんどん撤退していき、現存するメーカーでは当社が唯一とも云えるメーカーになりました。最初に売り出したバスダクトは、当時の協力業者に依頼し製造を行っていましたが、受注が少しずつ増加していき、自社工場建設の必要性を迫られたため、昭和36年5月に当神奈川技術センター(当時は相模工場)を立ち上げたそうです。市場が地域密着ではなく、全国を対象としたものであるため、高速道路を中心に考え、現在の東名横浜インターに近い場所にあった現在の大和市に行きついたとのことです。バスダクト市場は造船、自動車、精密機器、半導体、そして現在はデータセンター等の情報関連市場と時代の変化と共に変化して参りました。そしてそれぞれの時代の要請に応じた製品開発や事業拡大を図りながら、日本におけるリーディングメーカーとしてバスダクトの普及にも貢献してまいりました。
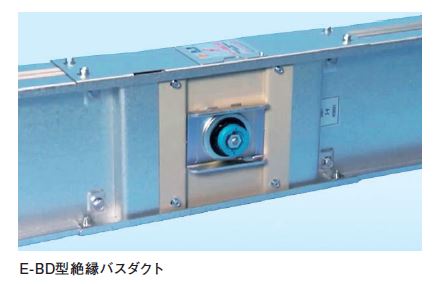
「フロアシステム事業」「環境事業」の概要についてもお聞かせください
上之門氏: 現在当社ではバスダクト以外の事業として「フロアシステム事業」「環境事業」を展開しています。「フロアシステム事業」は昭和61年(1986年)11月から販売を開始しました。当時OAフロアは床高100~150㎜の支持脚タイプが常識で配線するには重いコンクリートパネルを持ち上げる必要がありましたが、当社のフロアシステムではそれを数百グラムのカバーを外すだけで配線路にアクセスできるため、施工スピードも従来と比較にならないほどの時間短縮につながり業界の注目を集めました。(現在OAフロアとして業界のリーディングメーカーの日本のシェア第3位)また「環境事業」は2000年頃からの地球環境、都市環境の改善に対する社会的意識の高まりを背景として、社内における新事業を模索する中、屋上緑化事業が当社のニュービジネス構想として浮かび上がってきました。環境問題が注目される中、将来性が大きいなどの理由から、平成9年(1997年)3月に事業化調査と市場調査を開始し、平成11 年(1999 年)4月に軽量人工土壌、グリニッチソイルを使用したユニット式の芝コンテナを中心に底面かん水用のトレーとかん水システム等からなる「グリニッチガーデン」の販売を開始いたしました。現在では、様々なタイプの屋上部に使用できるようラインナップをご用意し、さらに壁面緑化も手掛けさせていただいています。
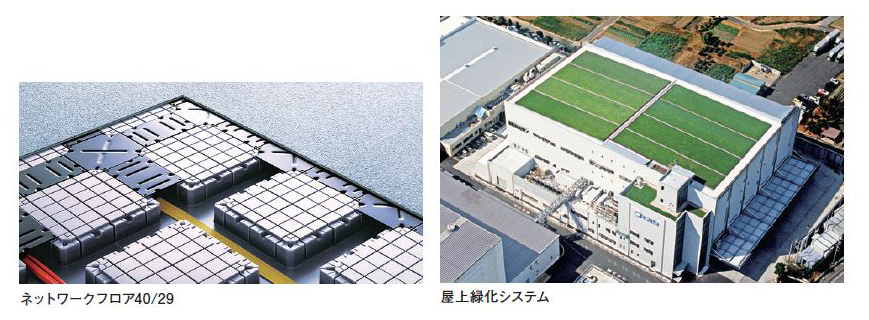
今回のコンサルティング導入の背景とはどのようなものだったのでしょうか?
島田氏: 2018 年末に新工場の建設用地が決定し、2020 年の春竣工を目指した計画が進行する中、鈴木がリーダー、私がサブリーダーという役割でプロジェクトに取組んでいたのですが、現在の当社には既存建物の一部リニューアルなどの経験はあるものの、一から新工場を建設するということへの知見やノウハウを持った人間が誰もいない状況でした。当時はまだ新工場の建設ということだけは決まっていたものの、具体的な中身が薄い状態だったので、中身をしっかりしたものにするにはどうすれば良いんだろうと鈴木と2人で色々考えながら、暗中模索の中で進めていました。そんな時、社長からこんなセミナーがあるから参加してみればと案内をもらったのが、現在コンサルティングを担当していただいている清水先生の「工場レイアウト設計セミナー」で、計画推進に自分達の力不足を感じる中、そのタイトル自体が光のように感じられ、セミナーに参加することにしたのです。参加したセミナーではプロジェクトを進める上で、これから特に必要性を感じていた工場建設のスケジュール管理に関する内容があって、清水先生にこの部分の資料だけでもいただけないでしょうかというような話をした記憶があります。清水先生の印象は製造に対する熱意がすごく感じられる方で、製造の色々な技術を世の中に広めていきたいという強い思いが、セミナーに1回参加しただけでも伝わってきました。やはりそういう熱意を持っている人の力は強くて、これから自分達の背中を押してくれるような印象を受けました。同時にセミナーで今後やらなければいけないことが膨大にあることが判って、それを自社の力だけで何とかするというのはかなり難しいものがあると感じました。
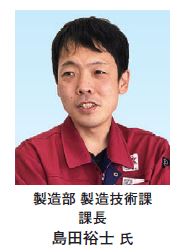
鈴木氏: 神奈川技術センターの生産性向上、老朽化、安定供給に向けたBCP 対策を含めた製造体制の確立が新工場建設の背景ですが、2019 年には過去最高のバスダクト製造量となり、全従業員に対する負荷が非常に高い状況となっていました。製造はかなり逼迫しており、お客様に頭を下げて納期交渉をしている姿を目の当たりにして、一刻も早くプロジェクトを進めなければと思っていました。
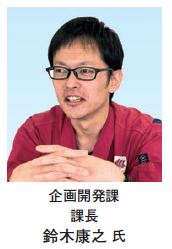
1日工場診断を受けられた印象はどのようなものでしたか?
島田氏: テクノ経営さんの1日工場診断は無料ということでしたので、当時のセンター長に相談して、その結果診断を受けることになりました。診断当日の印象としては、そんなところまで見られるのかというような、とてもドキッとするところがあって、これまで自分達ではムダと認識していないようなところを、これはムダですと指摘される。その理由が解らず、すごくもやもやして、その先を知りたいと思いました。それがコンサルティング導入へと進むきっかけとなったように思います。
鈴木氏: 私の方は当時生産量がずっと拡大している状況で、目の前のお客様の対応と平行して新工場の計画を進めるのが正直もう限界となっていました。その中で島田からセミナーでの話を聞いて、ほぼ即答でコンサルティングを導入したいと答えた記憶があります。まだコンサルティング費などが提示される前でしたが、後に費用が提示された時も自分は安いと思いました。新工場建設という非常に大きな投資に対して、しっかりと道筋を立ててもらい、新しい工場に魂を吹き込むための技術やノウハウを学ぶことができる。当時の上司と社長に対して島田と2人で、これは絶対にやらなければ駄目ですと頭を下げて直訴しました。社長は社員の熱意を汲んでくれる方なので、そういうことなら前向きに進めて行こうということになりました。そこからは一気に進み、すでに着工していて、スピード感が必要だったため、ご提案いただいてから契約までの期間は非常に早かったと思います。
上之門氏: 私は当時まだこのプロジェクトに関っていなかったのですが、以前から私自身も外部のコンサルタントの力を借りて、工場を変革してみたいという気持ちを持っていたので、良い話が来たという印象でした。それにしても彼らが短い期間で、200名ほどの人間を全体として同じ方向へ向かせて、新工場を立ち上げるというのは大変な労力がいることで、そういう取組みをタイミングとスキルを駆使しながら、非常に良くやってくれたと感じています。私自身も彼らのそういう姿勢には教えられるところがありました。
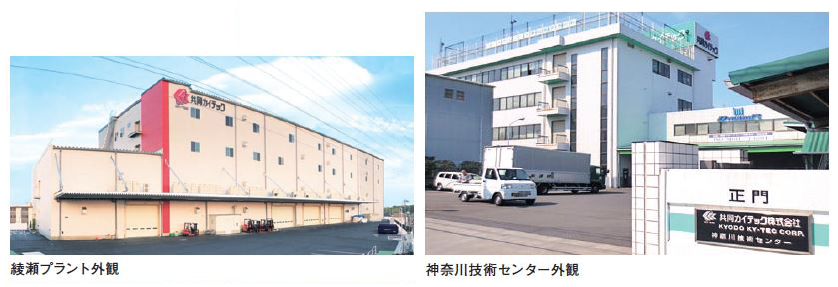
第1期のコンサルティング導入に関して社内の反応はどのようなものでしたか?
島田氏: これは人によって実に様々で、「何か新しいことが始まるのかな?」という期待感を持った捉え方をしてくれる前向きな人がいる反面、「外部からコンサルタントを入れても結局何も変わらないでしょ」というネガティブな反応もありました。ただ清水先生のコンサルティングの進め方は、まず初めに関係者全員の気付きの感度を上げていくというステップがあって、その取組みを行うことでプロジェクトに関係する社員が自分達の話を聞きながら進めてくれるんだという印象を持ちました。それまでは新工場建設プロジェクトといっても、実際にはコンサルタントと上の方だけで話をして進めていくのではというふうに思っていた人間が多い中、清水先生が社員一人ひとりの意見に丁寧に耳を傾けていただいたことは非常に効果的だったのかなと思います。今でも否定的な意見は一部にあると思いますが、全体的には会社が変革していることを好意的に捉えてくれている人のほうが多くなっています。やはり経験豊富な清水先生の進め方は非常にうまかったと感じています。
社員に向けた情報発信、共有などはどのように進められたのでしょうか?
鈴木氏: 今回の活動は当初新工場の立上げに関するものだけだったので、課長職ぐらいまでにはある程度の情報発信をしていましたが、具体的なコンサルティング内容などの情報共有を行ったのは後になってからのことです。活動は第1期、第2期、第3期という計画で進められていて、第1期については新工場の竣工に伴う活動であり、関係する社員も限定的でした。新工場の竣工は本来3月だったのですが、コロナや台風の関係で4月になりました。先程述べた通り製造が逼迫している状況だったため、遅れた分をいかに早く取り戻せるか、価値を生む工場にすることができるかが喫緊の課題となりました。そこで第1期のプロジェクトメンバーで検討し、7月に稼動開始という決定が成されました。以降の活動は時間との勝負の中で、当社の将来を担う新たな製造拠点を「魂の入った」ものにするため、第1期のメンバーで一致団結して取組みを進めました。そして7月に無事新工場が稼動した後、第2期の活動として神奈川技術センターの現場改善の取組みを進めることになり、このタイミングで初めて技術センターの全員に対して今回コンサルティングの具体的な内容や目標についての説明を行いました。
第1期の活動で具体的な手応えを感じたのはいつ頃だったのでしょうか?
島田氏: 当初気付きの積み上げを4週間程度行ったのですが、そこで新しい工場に対する要望や既存の工場の改善に関する現場の生の声が上がって来ました。社員から声が出てこないことには何を目指して活動していけば良いのか判断できないため、彼らから声が出てきた時にこれは何とか前に進めていけるのではないかなと感じました。その後、清水先生が理想的な製造工場に関する講義の中で、これまで当社の製造現場では否定的な意見が多かった「1個流し」の話をされたのですが、清水先生はその当社の状況を踏まえた上で、参加者全員を巻き込んで、色んな角度から討議、検討を行い、最終的には全員合意の元でポジティブな結論を出していただきました。このように様々な課題に対して、対話と検証を積み重ねることで、第1期の活動を推進することができたように思います。また自分にとっての第1期活動のターニングポイントは、新工場の2階のレイアウトを決定したところだと考えています。1階に関しては設備の関係などから制約があり、おのずとレイアウトが決まってしまうところがあったのですが、2階の組み立て工程以降のところは、1階とは逆に自由度が高く、どういう配置にするか、どういう流れにするかというところを一番悩みました。ただ稼動開始のスケジュールが決まっていたため、その段階での最適な判断を行うことを優先しました。そのため完成したレイアウトについて、自分としてはまだ改良の余地はあると考えています。活動全般を今振り返ると、第1期の活動メンバーは非常に積極的に1年間の取組みを進めてくれたと思います。
上之門氏: 当社ではこれまでにも、今回の活動での気付きと同じような意図で、提案活動などの取組みを行っていたのですが、社内には提案を出しても結局実現しないという諦めのような雰囲気があったように思います。それが今回の活動では提案したことが実際の形になるということを社員に示すことができました。それを鈴木君と島田君の2人が中心となり、色々な人が携わって実現できたというのは本当に大きな成果だったと思います。そしてそこで得たものが第2期以降の技術センターでの活動にも活かされています。
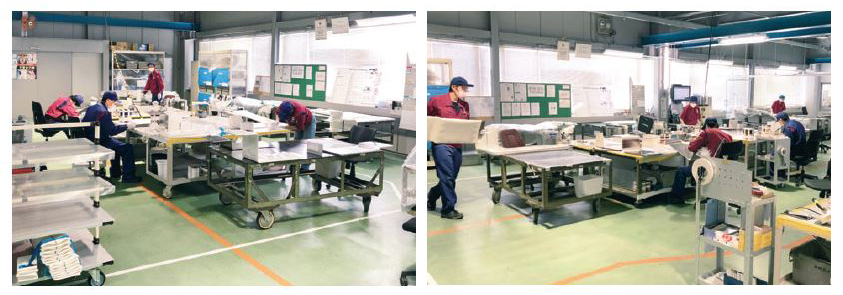
第2期の活動を推進する中で今感じていることを教えてください
鈴木氏: 自分自身も含めての話ですが、清水先生から理想的なものの流れなどについて講義の中で教えていただくのですが、「そうはいってもバスダクトにはこういう特性があるので現実的には難しい」というふうにどうしても否定的な見方から入ってしまうところがあります。特に社歴の長いベテラン社員の方などは、当然これまでのやり方に自負もあり、なかなか素直に聞いてもらうことは難しく、新しい視点で仕事に取組んでもらうためのきっかけづくりをどうしたらよいのか悩んでいます。ただ清水先生の話から、これまでの固定観念を振り払い、「製造とは何か?」ということを改めて考えた時、そこには本当に多くの改善要素があることがわかります。それを現場の人と共有し、進めていくために、ミーティングに参加してもらって、悩みや苦労していることなどをヒアリングして、それをベースに少し改善を行うことで、現場の作業がしやすくなったというような小さな結果を積み重ねることに取組んでいます。これを継続していくことで、目に見える変化が個人、チームの単位で現れてきており、製造現場が変化しつつあることを感じています。
島田氏: これは嬉しい悲鳴なのですが、実際この活動を通じて、製造技術としての自分の仕事が増えています。これまでだとこちらからヒアリングしないとなかなか出てこなかった現場の声が、積極的に「こういうふうにしたいけど、どうしたらいいかな?」というふうに出てくるようになってきました。この活動によって現場の視点が広がり、新しい仕事への取組み方につながっていることを感じています。
鈴木氏: これまでは現場の各チームそれぞれが、自分のチームのやり方というものに固執して、他のチームへの関心や繋がりが薄い状態でした。今センター長から各チームのチーフを集めて開催する「チーフ会」というものを任せていただき、各チームの連携を強化することに取組んでいます。この会では現場改善について、こちらから指示を出すのではなく、各チーフが自分で気付きを得るように誘導する形で進めていて、自分の課の4名の課員が同じ「現場視点」で各チームの現場に出向き直接話しをするなど、改善のサポートを行っています。清水先生は日頃折に触れ「製造現場で何が起きているかを知ることが一番重要」というお話をされますが、この活動を通じて、現場に寄り添うことの重要性を今まさに実感しているところです。
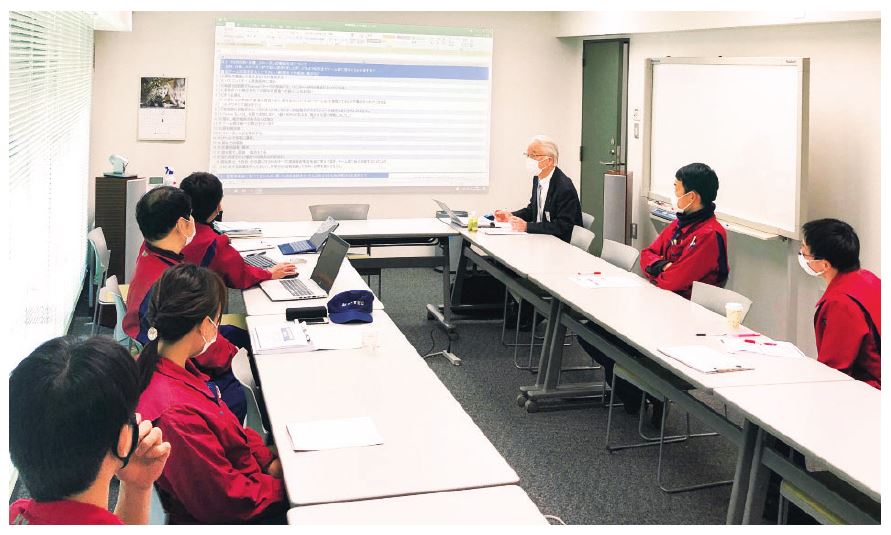
活動を通じた製造現場の変化についてはどのように見られているでしょうか?
上之門氏: 現場リーダーであるチーフという役割の社員は、普段から本当によくやってくれていると思っているのですが、これまでは細かな部分、製造で利益を生むために必要な取組みというような姿勢を見ることはなかなかできませんでした。報告でも良い報告や逆に悪い報告は上がってくるのですが、その中間部分で変革できる可能性がある部分についての報告はこれまであまり聞くことができませんでした。それが今の活動を通じて、鈴木君や島田君が彼らの意見や考えをうまく引き出してくれて、新しい気付きを得た各チーフの取組みに変化が見え始めています。そういうことからもチーフ会が核となって第2期以降の活動を推進していくスタイルが定着しつつあると感じています。
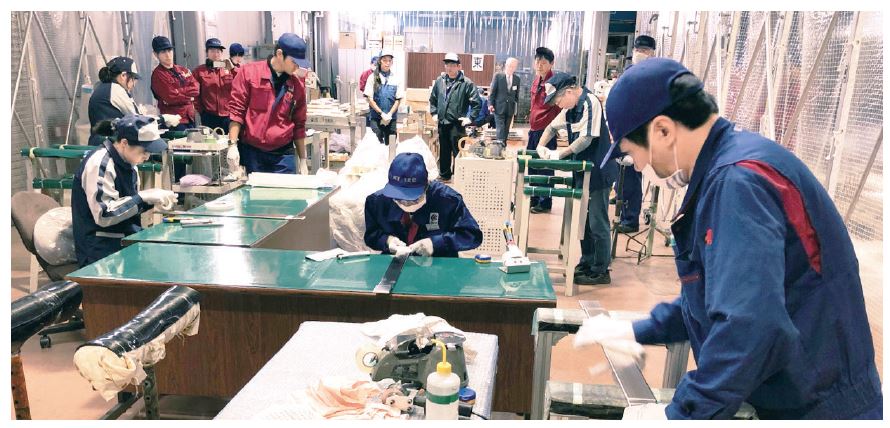
現場社員の意識について何か変化の兆しは見られるでしょうか?
鈴木氏: これまで現場からは「これはうちの仕事ではない」などの否定的な声を聞くことが少なからずありましたが、現在は前向きな声の方が多くなってきたような気がします。自分が現場に入ってちょっとしたテストなどをしながら、パートや派遣の方に「もう少しこうすると良くなるんですけどね」と一緒に改善をしていても「確かにそうですね」というような肯定的な意見をよく聞くことができるようになりました。気付きと言う形で現場の意見を吸い上げても吸い取りきれないものがあって、やはり現場に入ることの重要性をこれまでよりも感じています。そういう形で現場から実際の声を吸い上げる取組みを進めると、社員だけでなく派遣やパートの方からも、自分のチームの工程だけでなく、前後にも配慮したような発言が出てくるようになって来ており、これを今後も継続していくことで、もっと面白い意見や貴重な意見が出てくると考えています。
今後の活動の方向性についてお聞かせください
鈴木氏: 今後は主に工場における財務面の取組みを進めていきたいと思っています。これまでは最終的に数字を締め、今期は結果的にどうだったという感じの工場運営になっていて、数値的な指標がない中で漠然と残業時間を減らそう、というような形でやってきました。今後はしっかりした管理会計を導入して、計画的な工場運営を目指していきたいと考えています。また清水先生もよくお話されていることですが、前後工程の同期をしっかり行って、停滞品、ムダが無い工場の実現を目指したいと考えています。
島田氏: 製造技術として今一番にやらなくてはいけないことが、製造のものさしをつくることです。当社は超少量多品種ということもあって、おおまかにメーター数というものがものさしになっていて、バスダクトを月に何メートルつくるというのが一つの線引きになっています。ただ実際は品種、形状などで全然違うのに、メーター数という一つの目安でくくっていると、現場の人がどれだけ改善を行っても、測りどころがないため、やっていることに対して、本当に効果があるのか不安になってしまうと思います。そのためまずは製造のものさしづくりをしっかりやっていきたいと思います。それによって現場の改善成果が把握できて、新しいプロジェクトが入ってきた時に必要な工数とスケジュールが立てられるようになります。この指標が完成すると製造技術として自分の仕事の集大成になるのではないかと考えています。
最後に神奈川技術センターの今後のビジョンをお聞かせください
上之門氏: 当社は中小企業の中でも「強力な中小企業」というポジションに差し掛かっているのではないかと思っていて、中小企業の良いところは残しつつ、大企業にも負けない素晴らしい技術力も追求していかなければならない状況です。そういうことを踏まえて、残すべきところは残しつつ、変われるところはどんどん変わって行く。自分から前に進んで変わっていくことが重要で、そのための人材がどんどん育っていくような工場でありたいというのが、自分が考える将来のビジョンです。そのために現在のチーフを中心とした活動が、10年後、またそれ以降にも当社の製造技術をしっかり継承していくための礎づくりになっていけば良いなと考えています。また会社全体としては、全社員が経営の状態を見ることができて、全社員の力で会社を良くしていく。そんな時代の先端を走るような企業になれればと思います。
本日はありがとうございました
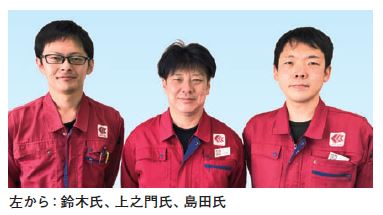
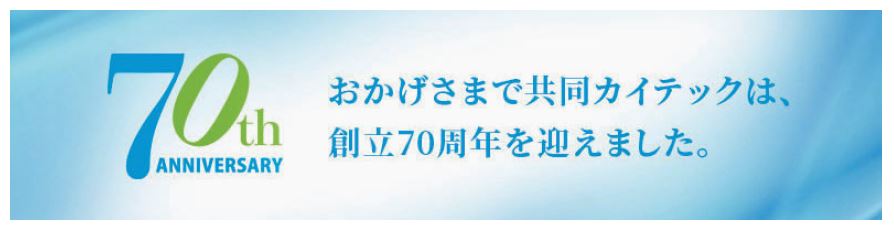
取材にご協力いただいた方
共同カイテック株式会社
神奈川技術センター 執行役員 センター長
上之門祐一 氏
企画開発課 課長
鈴木康之 氏
製造部 製造技術課 課長
島田裕士 氏
PDFダウンロード
【コンサルティング事例】 共同カイテック株式会社様