本ページでは、佐賀エレクトロニックス株式会社様に対するコンサルティング実績をご紹介しています。
弥生時代(約2千年前)の大規模な環濠集落跡である吉野ヶ里遺跡や、多彩な副葬品が発掘された三津永田遺跡・二塚山遺跡をはじめ、考古学的にも著名で重要な原始・古代の遺跡が多く分布する歴史深い吉野ヶ里町。この地で1965年に九州初の半導体後工程の工場として設立し、以降55年間に渡り、電子デバイス分野の環境が大きく変化し、グローバルな競争が激化する中、独自の技術により主にIC製品の組立・試験を展開しているのが佐賀エレクトロニックス株式会社だ。同社では多様化する顧客ニーズに最先端技術で応え、これまで蓄積してきた技術的優位性により経営基盤を確実にすると共に、新たなビジネス領域の拡大により、次代に向けた成長の種も芽生えさせている。今回の企業インタビューでは佐賀エレクトロニックス株式会社の改善活動の取組みについて、佐賀製作所 取締役 製作所長 蒲原 繁氏、 第一製造部 部長 永川 俊一氏、営業課 課長 羽倉 敏之氏、第一製造部 ウェハーテスト課 主任 納見 武氏からお話を伺った。
(※ASAP 2019年 4号より抜粋)
まず佐賀製作所設立の背景などについてお伺いできればと思います
蒲原氏: 弊社の創業は1965年ですが、親会社である新日本無線が、半導体の後工程を展開する工場用地を探す中、佐賀県知事が社長の大学時代の同窓であった関係から、同県への工場誘致を受け、人材面での人手の確保のし易さ、半導体の製造で使用する純水が地下水として豊富に存在していたことなどが要因となり、この地で創業することになったと聞いています。創業時はアメリカのレイセオン社(軍需工場)からダイオードトランジスタを生産するなど保税工場としてスタートし、1970年代に入ると新日本無線でICの生産が始まったことから、弊社の生産もIC製品に切り替わって行き、これが弊社の経営における最初のターニングポイントと言えます。当時、新日本無線の後工程の工場では、当社がメインの工場で、2000年代初頭のピーク時には月約1億3000万個のICを生産しており、従業員数も1,000名を超えていました。現在は使用していませんが、工場の敷地内には、女子寮や通信制の短大までの資格が取れる学校もありました。従業員の内、オペレーターは9割が女性で、佐賀だけでは充足しないため、近隣の長崎や熊本からも人を集めていました。当時の生産はまだ自動化ではなく、治具を使った細かな仕事が多かったため、女性向きの仕事であったことがその要因です。当時新日本無線の親会社であった日本無線が日清紡のグループ企業であった関係から、女性社員を生産の中心に置く紡績会社の工場運営のスタイルを弊社工場も受継ぎ、工場の作り方なども紡績工場を踏襲したものになっていました。
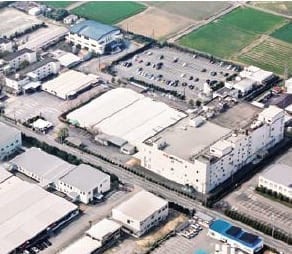
半導体業界の成長と共に順調に事業規模を拡大される中、経営状況が変化した要因についてお聞かせください
蒲原氏: 国内製造業全体の流れとして、1980年代後半から、円高の進行を背景に、生産拠点を移す兆しが見え始め、当時弊社のメインの顧客であった家電メーカーも海外に工場移転を進め始めたことから、後工程の自分達も海外拠点が必要だということになり、1989年タイのランプーン工業団地に新日本無線と共同出資で工場を設立し、1990年から操業を開始しました。以降汎用製品はそちらに生産をシフトしていくことになったのですが、タイの工場を拡張するため、当製作所のライン移管なども行われるようになりました。そして2008年のリーマンショックなどを経て、2011年からはその流れが本格化し、ピーク時には1000名を超えていた従業員数も、2014年には240名まで減少していました。タイ工場で汎用製品の生産を厚くしていく中、佐賀製作所では車載製品など技術的レベルの高い製品やOEM製品の生産に軸足を移し、新たなビジネスモデルの構築に取組み、以降その事業を拡大させてきました。現在当製作所には480名(請負、派遣を含む)が勤務していて、それにプラスして新日本無線からの出向エンジニアが50名いるため、全体で530名の従業員数となっており、ボトムの2014年から、人員、業績と共に、回復基調となっています。半導体の後工程を担当する企業は、吸収合併などでどんどん集約されてきており、同じ社名で55年間やってきている弊社は非常に珍しい存在です。その歴史の中、積み重ねてきた高い技術力が弊社の強みだと考えていて、特に小型、薄型の製品をハンドリングするような技術は国内の競合他社や、海外の工場でも真似できないものと自負しています。
今回のコンサルティング導入にはどのような背景があったのでしょうか?
蒲原氏: タイへのライン移管などで佐賀製作所の生産規模が減少する中、これまで弊社のものづくりを支えてきた多くの熟練作業者が退職することになり、属人性の高い作業が多い弊社の生産の基盤が弱体化していました。それが2014年をボトムにして、2015年から車載、OEM製品へのシフトを図り、また生産を戻していくような流れになっていったのですが、その中で人員を正規で戻すのは難しいという判断から、大部分の従業員を派遣で雇用することになりました。現状では派遣社員が5割、正社員が5割という人員構成になっていて、派遣社員は短い期間で移動する傾向が強いことから、これまでのような属人性の高いものづくりには限界があり、基盤も弱くなっていたため、その強化が必要になっていました。そのころOEM製品のお取引先企業がテクノ経営さんのコンサルティングを受けておられ、色んな改善活動をされているということを聞いていて、生産基盤の弱体化という課題を持つ弊社もそのコンサルティングを導入し、新たな工場の基盤を作れないかと考えていました。新たな事業として展開している車載製品の事業では、車の心臓部に関係するような製品を多く扱っており、昨今の不良品1個を出したら会社がつぶれてしまうような時代背景からも、品質に対するこだわり、感度の高い工場を早急に作ることが必要でした。そのためには何か仕掛けがいるということでそのヒントを求めて、テクノ経営さんのセミナーに当時の事業部長といっしょに参加することにしました。
これまでにもコンサルティング会社の指導を受けられたことはあったのでしょうか?
蒲原氏: 弊社では以前にも何度かコンサルティング会社を使っての改善活動は行っていました。当初その内容は主に間接部門のスタッフ中心の活動となっていて、課題である製造現場の改善活動には取組めていませんでした。そこで2016年から、5S、いきいき働ける人事制度、安全意識、マインド、モラル、モラールの向上による生産基盤強化を目指した「5UP SAGA」活動を始めました。これは生産管理、品質管理、設備管理、原価管理、教育の5つの管理力を上げるという活動と意味と英語のGo up(向上する)をかけ合わせたものです。また今年度からは「5UP SAGA」活動の一環で不具合品のゼロナイズを目指した「サザンカプロジェクト」という全社活動を立ち上げました。「サザンカ」は吉野ヶ里町の町花でもあり、花言葉には「ひたむきに努力し、困難に打ち克つ」という意味があります。
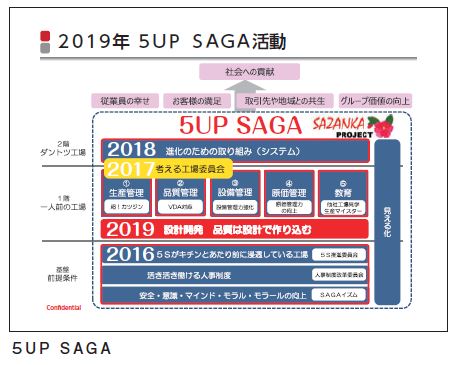
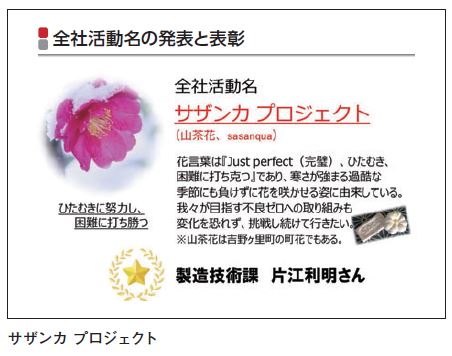
生産部門の改善に向けてテクノ経営にはどのような期待を持たれていたのでしょうか?
蒲原氏: 近年弊社では車載製品の生産に軸足を移した経営を行っており、自動車メーカーの方の佐賀製作所へのご来場も増えています。その中である自動車メーカーの方から、自分達は取引先である弊社を単なる部品供給先ではなく、自社工程の一部という認識で見ているとのお言葉をいただき、非常に感銘を受けました。それと同時に、そういう意味では弊社も、お客様の命を乗せて走る車の製造を行っているという意識を持って仕事に取組む必要があり、製造現場にもその意識を徹底させ、不良品ゼロに向けて、設備が常に淡々と動いていて、止まらない状態にしておかなければなりません。テクノ経営さんには、ものづくり現場での製造の意識向上を図っていただくことを期待し、コンサルティング依頼の検討を進めていました。テクノ経営さんのコンサルティングスタイルについては、既にテクノ経営さんのコンサルティングを導入しているお取引先のお客様から話を聞いていて、現場での改善活動という当時一番弊社の足らない部分に多くの実績があることも知っていました。そこでまず工場診断をしていただくことにしたのですが、その際、短時間にも関わらず、いくつかの業務上の無駄を見つけていただきました。その的確な指摘を聞き、現場での実情に長けていて、信用できると判断し、コンサルティングをお願いすることにしました。
コンサルティング導入にあたっての社員の方の反応はどうだったのでしょうか
永川氏: これまでも何度かコンサルティングは受けてきたので、コンサルティング導入については、それほど違和感はなかったと思います。ただテクノ経営さんのコンサルティングスタート時には、まだ別のコンサルティング会社の指導も受けていて、一方では5Sの指導を受けながら、もう一方ではC 改善の指導を受けているという状態であったため、現場としてはかなり負担がかかっていたと思います。また基本的に改善チームというような別組織ではなく、それぞれが通常業務との兼務で活動を行っているので、その意味からも大変だったと思います。そのようなオーバーラップの時期が半年ほどありましたが、現在はテクノ経営さんからのコンサルティングに集中できています。
2018年からスタートした1期目の活動を終えた実感はいかがでしょうか?
永川氏: 自分が一番気になっていたのは小集団活動ということについての社員の受け止め方です。弊社も以前はQC活動を行っていたのですが、2000年代に会社が低迷した時期、活動を中止してしまった経緯があります。以降小集団活動というものに対して、ある意味半導体業界の後工程全体がタブー化するような風潮となっていて、やらないほうがいいというような雰囲気がありました。現在も半導体の後工程を担当している会社で、小集団活動に取組んでいる会社は、意外と少ないと思います。半導体の後工程は装置産業で、良い装置が導入されると、現場の改善効果というのは意外と薄くなってしまいます。さらに装置メーカーが淘汰される中、どこの後工程の工場でも同じような装置が入ることで、似た状況が生まれ、小集団活動による実際の効果というのは、それほど望まれなくなり、そういう理由から活動を止めたというのが実情です。しかし業績が回復基調になって来た時、現場の人員を増やす中で派遣社員の比率が高くなっていました。正社員とは違うモチベーションを持っている人たちがいるという状況で、同じ職場内でのコミュニケーションや問題の共有化をどうするべきかという壁にぶち当たって、QC活動を復活させるかという考えもあったのですが、実際にはそれに1から取組むエネルギーも残っていない状況でした。そういう意味でテクノ経営さんからご提案を受けて、取組みを進めているC改善活動は、ちょうど弊社の状況にタイミングが合っていて、良かったと思います。小集団活動の本来の意味というのは、実利ではなく、みんなで話し合い、色んな意見を出して、部門内で知見を共有するということのほうが大きいため、C改善で、すごい改善を求めるわけではなく、まずは少しでもいいので前に進めていこうというのがスタート時の状況でした。もちろん大きな改善であるD改善にも取組んでは行くのですが、まずはC改善をこつこつやるということにメリットがあり、その取組みの中で、派遣社員の方の定着率が良くなったり、先々正規社員としての登用という効果も期待できるのではないかと思っていて、実際にその効果も出てきています。それがここまで1期の活動を終えての実感です。
御社の企業風土についてお聞かせください
納見氏: 社員像としては、非常に真面目で、すごく明るいというわけではありませんが、自分の意見をしっかり持っていて、とにかく真面目に仕事をこなしていくという人間が多いように思います。これは佐賀の県民性にも通じるような気がします。会社全体としては結束力が高く、何かテーマがあってやるぞと決めた時の力のまとまり方はかなり高いと思います。その力は過去幾度かの状況においても発揮されていて、以前いち早く生産革新を取り入れた際にも、その結束力は生かされましたし、そのパワーが現在のC改善活動の結果にも出ていると思います。
2 期目に入り、現在の改善活動の推進状況はいかがでしょうか?
納見氏: 活動の中心であるC改善にも目標値は設定されていて、それをノルマ通りこなせば、点数的には100点という形になります。今自分の部署のチームは3つのチームがあるのですが、その内2つのチームが一番高い点数の190点を獲得しています。前回のコンサルティングでコンサルタントの中川さんから、C改善のフォローアップの勉強会を行っていただいたので、その内容を自分から各チームのリーダー、メンバーにも伝えたのですが、その際も各チームから、とにかく1位をとりたいという声があがり、点数配分がある気付きメモ、改善のミーティング、改善の実施という項目で高い点数を取るため、メンバーの意見を積極的に聞いて、とにかく1件でも多く提出して1位を目指したいという意見を聞くことができました。そういう意味では活動が活性化され、取組む社員のモチベーションも非常に高く、良い方向に進んでいると思います。また1期目は改善活動のチームリーダーを実際の現場リーダーが担当していたのですが、2期目からは一般的なオペレーターの中から、活動のリーダーを選出して取組んでいて、その新しいリーダーを1期目のリーダーがうまくサポートしてくれることで、2期目のリーダーが主体性、責任を持ってチームをまとめていくことが出来ています。この活動でそういう人材育成上の効果も充分出ていると思います。またC改善では、点数配分を含めて、自分達で対策を実施するということが重要になってくるのですが、その際できるだけ定量的な成果、効果時間や効果金額というところを各チーム意識して出せるようになってきました。改善事例の提出物を見ても、1期目は各チームとも5S的なところできれいになったとか、整理整頓ができるようになったという定性的な視点が多かったのですが、2期目に入り定量的な効果を表す表現がだんだん増えて来ているので、より真剣にC改善に取組んでいるのではないかと感じています。
これまでの活動で事務局としての苦労したことなどをお聞かせください
羽倉氏: 活動をいかに浸透させるか、活動の内容、意味、目的を、事務局として社内にPRしていくことには苦労しました。C改善活動も最初はまだらな取組み状況で、提出物を出すところと出さないところの差が激しかったのですが、活動についての認知が浸透してきたことで、全員の意識が揃って同じレベルになってきました。活動スタート時には、事務局の私たち自身がVPM活動に腹落ちするまで時間がかかりましたし、手探りの部分が多く、浸透させることにも苦労しました。その解消に向けて、社員からの一つ一つの質問などに対するフォローを小まめにして行き、自分達だけで解決できない質問には、コンサルタントの中川さんに連絡を取り教えてもらうなど、出来るかぎりの努力はしたつもりです。また活動の浸透策として活動名称やスローガンを社内で募集し、活動名称「超!カツジン」、スローガン「チャレンジVPM! めざせ現場力UP!」が決定しました。この名称やスローガンにより、活動が一つの方向性に向かいやすくなったように思います。
今後の活動でどのような部分を強化したいとお考えでしょうか?
羽倉氏: この活動を始めてから1年間で自分なりに感じたことがあります。今までにも色々な改善活動には取組んできましたが、一つ一つの作業が面倒というのがあって、最終的にはそういう面倒くささによって継続性が失われて、活動が終わってしまう経験をしていたので、正直今回のVPM活動に取組む際も同じ繰り返しにならないかなと考えていました。改善活動を進める上で、指標として工場の稼働率を見ることが必要となるのですが、これまでの活動では、この工場の稼働率を出す上で色んな苦労をしてきて、活動が面倒になる大きな要因となっていました。ただ今回のテクノ経営さんのコンサルティングは人の稼働率、人の行動に着目するという視点がベースにあり、実はその人の稼働率と、工場の稼働率がほぼ合致しているということがわかり、これまで苦労して算出していた稼働率を3分の1程度の作業で似たようなものが出せるところがすごいと実感した部分です。こういう活動であれば、今まで面倒くさいなと思って停滞していた活動から脱却できてこれまでにない継続的な活動ができるのかなと思っていて、継続性ということを一番に意識し、それを実現できる活動の体制づくりを、2期目以降には取組んでいきたいと考えています。
最後に今後の企業ビジョンについてお聞かせください
蒲原氏: 目に見えるビジョンとしては現在新工場を作っていて、その新工場では車関係の新しいビジネスに対する設備が入ってきます。ボトムの時期からV字回復を実現し、さらに新しいビジネスの芽が出始めている状況であり、現状ではもうフロアがいっぱいなので、新工場の建設を決断しました。この工場もすぐにではありませんが、今お取引先からいただいている新しいビジネスの話で、2022年にはもういっぱいに埋まってしまう予定です。まずはこれら今の新しい動きを確実に達成していきたいと考えています。そのためにはこれまでの弊社の考え方を革新し、マインドセットを行う必要があり、そのための基盤を3年間で作っていきたいと考えています。中長期的なビジョンとしては自動車メーカーの重要技術を支える企業としての存在感を獲得していきたいと思います。
本日はありがとうございました
取材にご協力いただいた方
佐賀エレクトロニックス株式会社
取締役 製作所長 蒲原 繁 氏
第一製造部 部長 永川 俊一 氏
営業課 課長 羽倉 敏之 氏
第一製造部 ウェハーテスト課 主任 納見 武 氏