はじめに
経営者の皆様とお話をする機会に、よく聞かれるお悩み事の中に、「皆、まじめに仕事をしているのだが、提案が出てこない」、あるいは「もっと、自分達で考えて・気づいて・行動してほしい」という事が業界を問わず共通してあります。これらのお悩みに通じているのは、「いかに問題に気づくのか」、「いかに気づきから行動につなげるのか」という事がポイントになっています。
この日常茶飯事・職場の中で、皆さんの目の前に現われる「正常ではない状態」=「問題のタネ」、「不具合な現象」の多くは、見過ごされ・気づかれずに、「問題に発展して顕在化」するまで取上げられないのが、よくある現場の状況になっています。
今回は、この見過ごされている状況をいかに「とらえて・取上げて」ゆけば、気づきと・行動につながるのか、という点についてお話ししてみたいと思います。 そこには、①「なぜ、気づかないのか」というコトと、②「実は気づいているけれど、行動しない」というコトの2つの面があります。
なぜ、気づかないのか
①の「なぜ、気づかないのか」という理由には、「問題を回避する心理」が働いていて、ほとんど見えないでいる、あるいは「固定観念の中にドップリと漬って」、見ていても何とも感じないなど、いろいろと考えられますが、これらの状況を打破するために「問題のとらえ方」という方法があります。
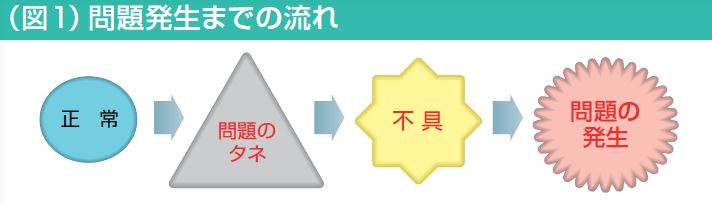
(図1)に模式図をあげておりますように、問題に発展する以前に少なくとも2つの状況があるという「見方・考え方」を持つということが出発点・突破口の入り口にあたります。
このように、「いきなり問題が発生する」わけではなく、問題の前に「問題のタネ」と「不具合な現象」があるのだな…というように理解していきます。
ケース1「何でも、問題だ!」と慌ててしまう
ある朝、フォークリフトのスタートキーを回してもエンジンがかからない!→バッテリーがあがってしまった→さあ大変だ「これは大問題だ!!」→と慌ててしまい大騒ぎをしてしまった。
このようなケースは、「まだ問題にはなっていないよ」、フォークリフトが動かないのは、「不具合な現象なんだ」ととらえることがポイントになります。このように落ち着いて、あらためて考えてみれば、様々な問題回避の方法が浮かんでくるものです…「今日、暇そうなフォークリフトが無かったかな?それを借りられないかな」など、慌てずとも済ませる方法は見つけられるようになります。
ケース2 「 問題のタネ」が見逃されて、問題になってしまった 朝礼で、「昨日、仕事中に(安全面で)ヒヤリとしました」との報告がありました。設備の運転中に、ホコリを落そうとエアーガンで吹いていたところ、先端のノズルが外れて落ちてしまい、トッサにそれを押えて・つかみましたが、危うく手を挟まれるところでした…という、危険なヒヤリ報告であり、このようなケースは、たまたま問題になりませんでしたが、「一歩まちがえば問題だった」と考えましょう。
その後の検討では、「そういえば先端のノズルは、かなり前から、緩んでいるのに気づいては何気なく手で締めて、それで終っていたな」という意見が出てきました。
これからは、ノズルのゆるみのような「些細なこと」も災害・不良などの「問題のタネ」になるのだととらえて「緩み止めをするなど何か手を打ってゆこう」と考えていけば、自分達でも実施できる行動につながっていきます。
ケース3「 変だな」と感じるが、それが何なのかハッキリしない
若い構内協力会社の方でしたが、朝礼の場で「現場にある廃棄物の投入口なのですが、ちょっと気になるのです」という発言がありました。
皆さんと現場に行って、見ながら聞いてみると、「何の表示も無いことが気になる」ということでした。この時、周りにいた方は、ほとんどがベテランの社員さんであり、「こんな投入口に何の問題もないよ」というように皆さんは受取っている様子でした。
若い方が気になるところを、なぜ・なぜとお聞きしていくと、「何でもかんでも、社員さんから渡された物を捨てていれば、それで良いのでしょうか?」という大変に大切な疑問を感じていたのでした。
「そうですね、あなたは投入してはいけない物があるのではないかと心配をしてくれていたのですね」ということに、社員さん達と共に分かってきたのでした。
この日の結論としては、「投入口に入れてはならない物(水、油)を掲示する」ことに決まりました。
このケース3は、大変に貴重な事例です。それは「危険予知・トラブル予知」をしてくれた例だからです。
誰もが見過ごしてしまう「表示がないこと=問題のタネ」に対する気づきと、そこから生まれた対策が、廃棄物容器への異物質混入を防ぎ、産業廃棄物処理費用単価アップを防ぐ「予防処置」になった事例でした。
これら3つのケースのように日常茶飯事、目にすることを、「これは、何だろう?」「問題か・現象か・問題のタネか?」ととらえて・考えてみることは、現場第一線の皆さんにも充分できますし、意外に面白がって、日常会話の話題になっている場面が多く見られるものです。
ここまで「なぜ、気づかないのか」ということについて考察してきましたが、「問題のとらえ方」という見方・考え方を知り、使ってみることで、興味を湧かし・皆さんと会話するきっかけとしていくことで、今まで見逃していた・気づかなかったことが見えてくるようになります。
なぜ、気づいているけれど、行動しないのか
現場で「なぜなぜ問答」の実践指導をしている時に、この質問を第一線の皆さんにお聞きしてみることがありましたが、「なぜ・なぜの6~7回目」あたりに、「言えば自分だけがやらされてしまう…だから言わないのです」という場面が、業界を問わず共通して出てくることが何回もありました。
「言えば自分だけがやらされてしまう」という状況は、
①改善活動が個人的だったり、グループ単位で取組むということだけが決まっていて、バラバラな状態で放任されているなど、全体的な活動展開になっていない
②「誰が問題を取上げ」、「誰がその原因を考え」、「誰が対策を実施するのか」などの役割分担がハッキリしていない(あるいは、発言者にすべてが任せられてしまう)
③実は、日常の問題は沢山あるが、どれから・どのように手をつけたらよいのか、その進め方がわからないなど、「皆さんの気づきや、やる気が引出せない状態」で運営されている会社が、大変に多いのも現実であります。
このような状況を打開する方法としては、会社ごと・職場ごとの文化や風土によっても異なるのですが、
①全員参加型の改善活動を立上げ、工場・会社全体の取組みとして推進する
②現場だけがやらされる活動ではなく、場合によってはスタッフ・管理者が手伝う仕組みをつくり、実践する
③グループ1件など、具体的に目標件数を決めて、問題を取上げ、解決していく
などが業界を問わず、成功への共通ポイントとなっています。
(図2)のグラフは、組織人員175名のある会社における「日常問題解決活動に関する実績」ですが、前述の3つのケースをはじめ、多彩な日常の問題を取上げて、日々・1グループ(約10名)あたり・1件の目標件数を掲げて取組んだ活動の事例です。
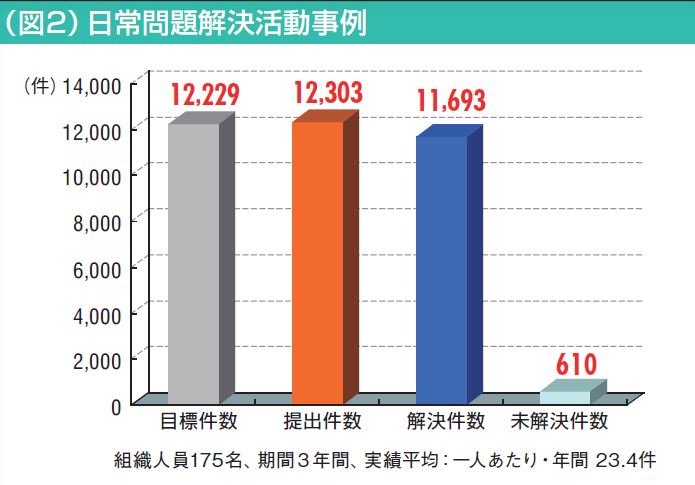
以上のように、「問題のとらえ方」、および「全員参加型の改善活動展開」により、見過ごされ・気づかれずに「問題になって顕在化」しないと分からなかった『問題を未然に取上げ』て、小さな「問題のタネ」のうちに、自主的に自分達で実施できる対策を打っていくことが出来るようになります。
組織事故の予防効果
これまで説明してまいりました、現場の基本的な日常管理・改善に関する活動は、継続的に・全員参加で実施していくことにより、「不安全行為」「作業現場要因」「組織要因」などを変えていく地道な活動となり、組織事故の対策につなげることも可能になります。
あとがき
携帯電話など日本の製品やサービスが海外で通用しない現象を代表例として「日本のガラパゴス化」というキーワードで警鐘がならされる機会が増えてきています。
一方、NHK大河ドラマ「龍馬伝」の舞台となっている明治維新につながるこれらの時代には、「鎖国状態」から脱皮していくために、日本はこのようにモガキ苦しんでいたのだということを、映画仕立の映像表現の中で教えてくれています。
「ガラパゴス化・鎖国状態」という視点で、企業・工場の中を見渡してみれば、少なからず「タコツボ状態」になっている部署やグループ・個人は存在している状況が、実は大多数の組織に共通していることではないでしょうか。
千里の道も一歩からと言いますが、その一歩目が「問題のとらえ方」というのは、けっして大袈裟ではないと、企業様との活動経験の中から小職は感じております。
このたびは、この特集欄をご一読いただきまして、まことに有り難うございました。