技術力の質的転換で世界に勝つ!
技術者育成を置き去りにしてきた
現状の製造メーカは、円高、リーマンショック、自然災害などの多くの困難から立ち直り、また以前の企業力を取り戻したように見える。 不採算製品や部門の切り捨て、海外安価生産地への移転、さらには人員の整理など、企業存続最優先の手段が取られてきた。
2013年に入って、円安、アベノミクス、オリンピック開催決定などで景気上向き(気分)になり一息ついている製造業もあるのではないだろうか。 実際、設備投資は上向き始め、景気判断も上向きになっている。企業は財務的指標は形が付いてきたがその代償に大きな課題を置き去りにしてきた、それは人材の育成である。
失われた20年は人を育てることを犠牲にしてつくろってきた部分がある。 2012年まで20年間、製造業に働く人の平均年収はずっと400万円ほどで実質上昇はゼロ。減少した人もいる。 何とか人件費のコスト高を抑えるため人員削減、派遣社員やアルバイト採用などの手を打ち、人への投資は全くと言っていいほどなされて来なかった。 犠牲にしてはならない奥の手を使ってしのいできたのである結果、人が育っていない、ノウハウ伝承ができていないという深刻な課題を生んでしまった。
「企業は人なり」は日本の力
技術者は自動車、IT企業に集中していて、これらの企業では技術者の就業者比率は15%であり米国並みとなっている。 しかし、一般の製造業の技術者数をみてみるとかなり少なく、約5%で米国の半分に過ぎない。
今更、社内で技術者は増員できない、かといって新規、中途採用すれば経営上辛くなる。 技術者不足は、息の長い先行投資不足で、新技術開発、生産技術改革遅れにつながり企業の発展はおろか継続すら危うくしてしまう。 日本企業の良さ、強さが失われてしまう。 この状況にどう対応するかがこれからの10年で勝ち組になるかならないかの分かれ目になるといってよいだろう。
増員しないで技術者不足を解消するにはどうすればよいのだろうか?
仮に業務の効率化を図り、リードタイムを短縮することがそれぞれ25%改善されれば 1.25×1.25=1.56 なので、計算上50%の人材が生み出せることになる。
さらに技術者の質向上を図ることで、実質的に技術者増の効果を生み出す方策が重要で、この3点セットを明確な ターゲットにした投資が望まれているのである。
人への投資とは何なのか、いくつかの例示で説明しよう。
仕組みの問題顕在化
製品開発から立ち上げ、あるいは納入までの期間に起こる「品質問題」や連携ミスによる「手戻り」ほど技術者工数を無駄にするものはない。 個別対応は当然にしても抜本的対策を打たなくてはいけない問題を、プロセス不良と考えて「問題発見MAP」を使って分析する方法を述べよう。
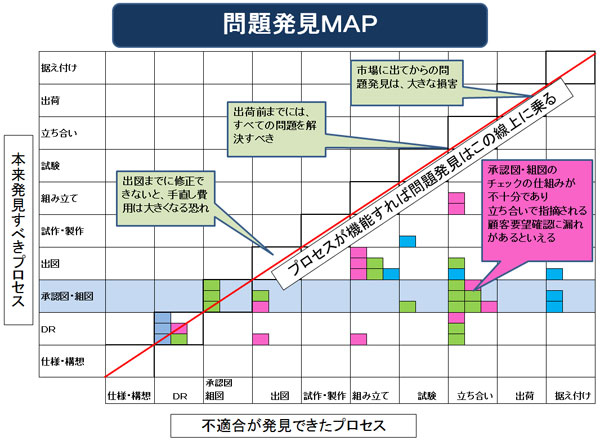
縦軸横軸に受注から納入までの業務のプロセスをとる。
過去事例で、市場の品質問題、設計・製作時の問題を洗い出し、その問題の発見されたプロセスを横軸、発見すべきプロセスを縦軸にとる。 例えば、「組み付かない」問題は試作(組立)工程で発見されたら横軸は「試作」、図面チェックで発見しなければならないことであれば縦軸は「図面チェック」のところにプロットする。 こうして出来上がったのが「問題発見MAP」である。
縦軸の発見すべきプロセス毎で集約すると、問題の大きいプロセスが見えてくる。 発見すべきプロセスでの仕事の仕組みのどこの問題があるか、仕組みを見直し改革することで手戻りを改善してゆく。
この例では、前段階での業務が不十分であることが原因となっている。フロントローディング即ち前工程の改善を進めることが解決につながる。 「顧客要望の確認」が改善の必要なプロセスである。
現状の仕事のやり方を分析し「漏れ」をいかに防げばよいか、効率よく吸いあげるにはどうすればよいかを見直すのである。質の向上はどうすればよいのだろうか。
「技術伝承、ノウハウ」の問題
技術者における技術伝承というと、重要なツールは図面、技術標準、社内規格などが代表例になる。
殆どの企業は各種議事録や、DR、計算書、生産にあっては作業マニュアルを作成して技術伝承をしている。 いずれも「結果伝承」ではあっても「技術伝承」にはなっていないことにお気づきだろうか。
新規の設計や未経験領域では役に立たず、また類似問題を起こしてしまうことがままある。 多くの不適合問題は新しいが技術的には再発に近い。図面やマニュアルでは模倣する事はできるが解析・創造する技術は伝承されないからである。
伝えるべきは結果としてのドキュメントだけではなく結果に至った「原理」と「原則」なのである。原理とは自然の摂理であって、原則はそこから導き出された自社のノウハウを指している。
解りやすい例でいえば、ドキュメントに「3mm隙間を設ける」と記載がある場合「金属には熱膨張収縮がある」のが原理で「異種金属接続には隙間を設ける」のが原則である。そして図面上の寸法の「隙間3mmを設ける」が結果である。結果だけを伝承するから抜けが出る。
わかりきっていると思いがちな「原理」「原則」を伝えることが重要なのである。 原理と原則を伝承することで従来のノウハウは飛躍的な拡がりを持ってくるのである。技術者が伝承されたドキュメントの真の意味合いを習得することで、質の向上が図れるのである。
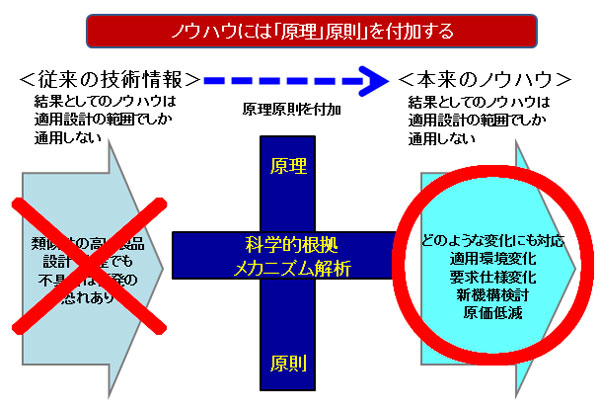
人材不足の解消
日本の企業とりわけ製造業にあっては、人を賃率だけで計算し、損得を勘定しがちである。
後進国との決定的な有意差である日本人の質の高さを踏まえた人材育成をすることで数倍の効果がもたらされる。
技術者育成には、(1)業務効率化、(2)リードタイム短縮、(3)質向上の3点セットに重点を置き、自社のもっとも緊急な課題から改革に取り組み、人材を量でなく質で捉えられるように変革するとよい。
開発技術や生産技術力が、工数でなくスループット量で語れるようになれば本物である。
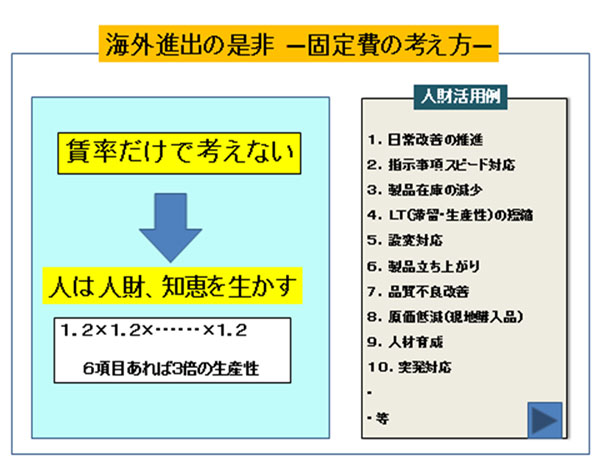
以上