はじめに・・・
過去から未来に向う時間軸のなかで推移する今をどうとらえるか。それを可能にするのが「指標」であると[前編]にて申し上げました。後編では、改善ツールとして「指標」を活用するための活動ステップについて管理図を中心にお話しします。
5.指標は掲示物ではなく改善のツールであることを認識する
多くの企業、工場で見かける光景です。日々の生産結果がグラフ化され壁に掲示されています。しかし誰も見ていません、誰も掲示してあることにも気づいてもいません。 これでは指標の機能を全く果たしていません。また指標はあるが活用できていないといった声もよく耳にします。原因は指標の機能役割が充分に理解をされず効果的な運用が出来ていないことにあります。
生産現場における日々の管理指標をまとめたものを一般的には管理図とも言いますが、管理図を基軸とした改善行動は以下のステップで進められます。
Step1.本日の実績を記入する (管理図や管理グラフへ事実を記入)
Step2.数値の変化や推移を見る(全員が興味を持って見る=事実の共有)
Step3.管理図から気づく (変化/異常に気づく、数値に疑問を持つ)
Step4.管理図から考える (変化の原因や要因を考える、分析する)
Step5.管理図から決意する (Plan:改善課題として解決しようと決意する)
Step6.管理図から行動する (Do:解決のための行動する)
Step7.管理図から結果を見る (Check:改善結果や効果の検証する)
Step8.不具合の是正/標準化 (Action:不具合修正/標準化や仕組み化する)
Step1~5の領域を問題形成といい問題を問題として認識して改善を決意することです。Step5がPDCAのサイクルを回すための起点Pになります。Step6~8を問題解決のための改善行動と呼びます。 問題形成領域で求められるのは気づきの感度と力です。つまり、常に問題意識を持ち改善すべき課題(P)を出し続ける力です。改善行動(DCA)で求められるのは問題解決(結果を出すまで)のスピードであると言えます。
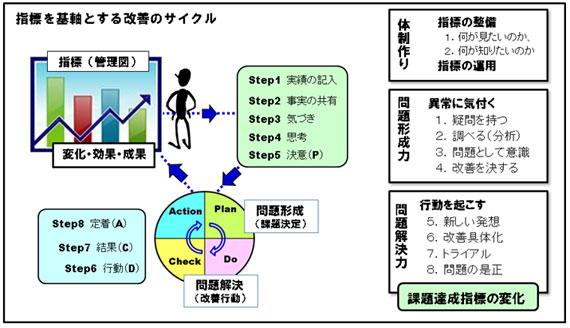
現場を見ることでムダを見つけ、見つけたムダを排除する改善のやり方は、現場ムダ取り活動とか眼力改善とも呼ばれます。これは職場環境整備に有効な方法ですが、前述したように、改善の目的は工場の数値を変えることです。 現場で目についたムダを取るだけでは、経営TOPが求める数値を実現することはできません。
6.階層や用途によって指標を使い分ける
指標には最上位に位置し、コストというモノサシで測る経営指標があります。その下には各部門や職場ごとに職場管理指標があり、モノサシとして時間(工数)と量(出来高)、これに基づき変換された各種の指数が指標として用いられ、管理図として掲示されます。また改善活動においては、進捗管理や達成度確認に用います。気づきを中心とした現場の小改善では改善件数と改善率といった指標を用います。
最後に・・・
指標とは定量的数値で表された客観的事実です。この指標を基軸とし、指標を観つめ、指標から気づき、指標から考え、改善を決意し行動を起し、各階層や職場の水準を上げ、それぞれの改善活動の成果が最終的な経営指標であるコストに収斂し更に変えて行くことが真の改善活動なのです。 指標を整備して上手く使いこなすことが改善活動で確実に成果を出すポイントです。
以上