はじめに
故 大野耐一氏により執筆された書籍「トヨタ生産方式-脱規模の経営をめざして-」が出版されてから30年以上も経ちます。この本により、ジャストインタイムを達成するための“後工程引き取り生産”が一般的なものとなりました。
恐らく現在までに、多かれ少なかれほとんどの企業がこの後工程引き取り生産にチャレンジした経験を持っているのではないでしょうか。ただし、実情を見る限り、多くの会社ではこの後工程引き取り生産を本当の意味で活用できていません。なぜでしょうか。
テクノ経営では生産現場の改善を数多く支援してきましたが、事例研究に学ぶ意義は大きいと考えています。そこで今回は、なぜ多くの会社で後工程引き取り生産がうまくいかないのか、意外と知られていないトヨタ自動車内のプレス工程における生産方式の発展の歴史と共にひも解いてみます。
1.ロット生産工程における“後工程引き取り生産”の基本的な考え方
後工程引き取り生産における“生産指示形態”の基本は、信号かんばん(三角かんばん)(※)です。これは、一定の基準在庫になったら仕掛け指示の役目をするもので、かんばんの外れた順番にロット生産を行ないます。
※信号かんばん・・・
段取り替えに若干の時間を要するプレス、ダイキャスト、樹脂成形等のロット生産工程での仕掛けに用いるかんばん。三角形をしているので 通称三角かんばんと呼ばれる。
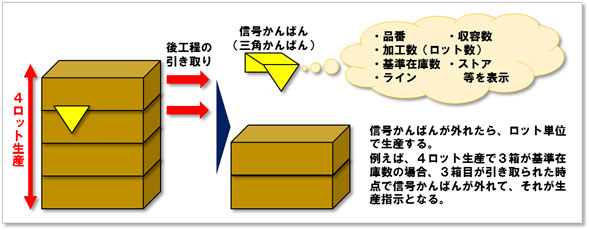
言い換えれば、この信号かんばんは全製品を“定量不定期に” “後補充する”生産方式です。
2.ロット生産工程における“後工程引き取り生産”の問題点
まず後工程引き取り生産の生みの親であるトヨタ自動車の「プレス工程」の事例を基に説明します。プレス工程の究極は1個流しですが、現在でも未だロット生産が基本です。このプレス工程では、信号かんばんによる後工程引き取り生産が次のような変遷を辿ります。
(1) まず、初期段階は少種多量であり、現在よりはるかに大ロット生産が行われています。
(2) その後、ニーズの多様化により車種数が増加します。これに伴い、1ラインに引き当たる部品種類数も増加します。
(3) また、注文のバッティングが発生し、納期の制約も増えていきます。
(4) そこで、段取り改善により小ロット化を進め、その状況を克服していきます。
(5) しかし、世の中のニーズは更なる多様化へと向かいます。多種少量の時代の到来です。
(6) そして、多種少量に加え、顧客の短納期へのニーズは益々強くなります。
(7) ここまで来ると、これまでの信号かんばんによる生産方式では、人間が個々の在庫状況を見ながら、「まだ間に合う!」「そろそろ危ない!早く仕掛けよう!」と判断しながら作業を行なうようになります。
(8) これに拍車を掛け、世の中からは更なる多様化ニーズが迫りますが、段取り改善のスピードは市場ニーズに追い付けない状態になります。完全に行き詰まりです(Oh , no・・・)。

このように、基本的には“シングル段取り”や“ゼロ段取り”によって時代のニーズに合わせて改善を進めていかなければいけないものの、さすがに市場の要求スピードが早く追い付けない状態になりました。
ロット生産の工程を持つ場合、このトヨタ自動車の例と同じ状況の会社は沢山あると思います。色々な企業の状況を聞く限り、この状況に陥った際に経営トップが取る対応は3つに分かれるようです。
(1) 「この生産方式は自社に合わない」と言って大ロット生産に戻してしまう。
(2) 「この生産方式が理想に決まっている」と言って段取り替えばかりやらせている。
(3) 「どうしたら自社に合った生産方式が出来るか」引き続き考え試行錯誤する。
貴社の場合は(1)~(3)のどの対応を選択されるでしょうか。
次回は、(1)、(2)の対応を取った時のデメリットと(3)の対応を取ったトヨタ自動車のその後についてお話したいと思います。