はじめに
前回は、ロット生産工程であるトヨタ自動車のプレス工程を事例に、後工程引き取り生産により発生した問題点をお話ししました。今回はニーズに対応する改善、生産方式の進化が求められる背景についてお話します。
前回の最後に、後工程引き取り生産が市場ニーズに追い付かなくなった時の対応について質問しました。
(1) 「この生産方式は自社に合わない」と言って大ロット生産に戻してしまう。
(2) 「この生産方式が理想に決まっている」と言って段取り替えばかりやらせている。
(3) 「どうしたら自社に合った生産方式が出来るか」引き続き考え試行錯誤する。
まず、(1)を選択した場合は当然、市場ニーズとは真逆の方向に進むことになります。 顧客からは小ロットの注文しか来ないのに大ロットでしか生産が出来ないため、いつの間にか倉庫は在庫だらけ、死蔵品も大量に抱えることになります。 その結果、キャッシュフローは悪化し、在庫の管理工数も膨れ上がります。これは一番やってはいけない対応です。
(2)を選択した場合は、受注に対して定時操業では当然時間が足りなくなります。その結果、毎日何時間もの残業、休日出勤が常態化し、社員のモチベーションは限りなく低下していきます。 また、原価に占める工数比率も上がってしまい、価格競争力も低下します。この対応も避けなければいけません。
従って、永続的に生き残るためには、やはり(3)を選択せざるを得ません。 では、トヨタ自動車の事例に戻って、(3)の対応によりどのような生産方式が生まれたのか確認していきましょう。
3.行き詰まって生まれた、生産方式の“カイゼン”
もしも、段取り改善が時代のニーズに追い付き、更なる小ロット生産(究極を言えば一個流し)対応が可能になれば、信号かんばん(三角かんばん)のような定量不定期の生産指示形態で全く問題はありません。 しかし、理想と反して、この段取り改善スピードが時代に追い付かなくなったのは紛れもない事実です。その改善策として生まれたのが、定期不定量・定量不定期方式(以降、定・定方式と呼びます)です。
この定・定方式では、下記のように、売れる特性を2種類に分けて、生産を行なうことにしました。
◆ 定期不定量(=多量)
・・・「とりあえず一定のタイミングで期限を切り、そこまでに売れたものを造る」という方式。つまり、指定席化しパターン生産(決まった時間に売れた分だけ生産)を行ないます。
◆ 定量不定期(=少量)
・・・「売れた量をその都度造ると生産性が悪化するため、ある一定量が売れるまで待ち、その量に達したらまた造って補充する」という方式。こちらはある一定量が売れるまで待ち、ロット形成されたら自由席で生産を行ないます。
これらの基準量を決定し、毎月P-Q線図からロットサイズの決定等を行ない、指定席・自由席のパターンを作成します。
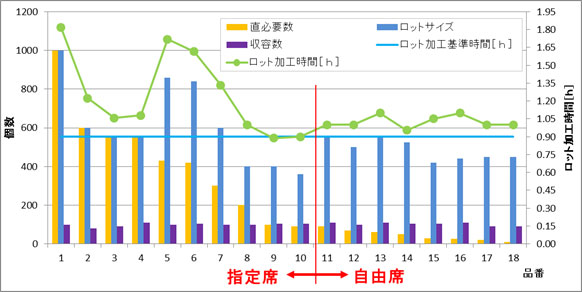
以上の方式で生産を行なうことにより、在庫が“適正化”され、かつ出来高アップに繋がったことで、総費用の低減になりました。 もちろん在庫量は、段取り短縮等の改善を行ない、実力を上げながら低減していくことは並行して行わなければいけません。
なお、1品1葉の完全受注生産の場合は、これに1品不定期が加わることになります(補用品等が該当)。その場合は営業サイドの情報も入手し、ロット形成の可否を慎重に検討していくことも必要です。
4.生産方式は日々進化するもの
この定・定方式は、日々進化しています。つまり、レベルアップ・ヒストリーがあるのです。言い方を変えると、社員が日々進化させるために頭を悩まし続けているのです。
この定・定方式は、90年代中盤に導入がスタートしています。それから10年弱の期間を経てようやく他工場へ展開できるレベルにまで達しています。 そして、その後システム化等も進め、グローバル標準を構築する取り組みも行っています。この標準化を含めた生産方式レベルアップの取組みも実に5年以上の時間を費やしています。 恐らく、今現在も更なるレベルアップに向けて、日夜試行錯誤を繰り返していることでしょう。
この事例は、生産方式の構築は1度きりではなく、永遠に継続していくテーマであることを教えてくれています。 後工程引き取り生産の生みの親であるトヨタ自動車でさえ、長い年月を掛けて試行錯誤をしているのです。ましてや、それを真似しようとしている会社が1~2年程度取り組んでうまくいかないからと言って諦めるのは、 チャンスを自ら投げ出していることと同じです。
生産方式の改善は元より、あらゆる改善は、「描いた理想をいつか絶対やり遂げるという強い意志で遂行する」ことが重要であり、これがトヨタ式改善の一番の教えであるのかもしれません。
5.最後に
以上のトヨタ自動車の例からも分かるように、自社が置かれている現状の課題を克服する“新しい生産方式”の構築は、1~2年で簡単に達成できるものではありません。 ましてや、どこかの会社の生産方式をそのまま自社に当てはめれば上手くいくという考え方では、成功する可能性は非常に低いと断言せざるを得ません。
大事なことは、ジャストインタイムの基本的な考え方である「必要なものを必要な時に必要な分だけ造る」ことから大幅に逸脱することなく、 今獲得できる利益を“確実に獲得できる生産方式はどういう形か”社内の人間が中心となって本気で考え続けることです。
テクノ経営が提唱するVPM (Value Producing Management)は全員参加を基本に付加価値を高め、利益につながる自社流の改善・改革を支援しています。 流儀や形式にこだわらず各職場のスタンスで取り組める実践的な活動こそ功を奏すると考えるからです。
ただ作業が辛くなるだけの改善など誰も進んでやらないですから。一気に80点を狙わず、初めは40点でもいいと思います。 その40点を60点、80点に上げていく過程で、必ず社員は成長していきます。 もちろん、初期の段階では、社内の有識者やコンサルタントを活用し、大きな方向が間違わないように進めていくことが大切です(この段階では、 色々な事例から判断できる人物がいた方がスムーズに行きやすい)。ただし、最終的に社内の人間だけで生産方式の改善が続けられなければ、 いつの間にか後戻りしてしまいます。自主改善の土壌づくりには推進リーダーの育成が不可欠です。自社流の生産方式は一朝一夕に構築できません。 そして生産方式に完成形はなく、改善に終わりはありません。より良い状態を目指して常に進化を続けるのが製造業のあるべき姿です。
「短期間で見栄え良く出来上がったけれど、ただ理想を当てはめただけなので、歪があちこちにある生産方式」
「時間は掛かったけれど、働いている人が意図を理解し納得できている生産方式(しかも次世代リーダーが育っている)」
貴社はどちらを目指しますか?