保全マン任せにしない仕組みづくり
設備のあるべき姿とは、機械設備が持つ性能をフルに発揮し、100%の生産性でモノづくりができる体制です。つまり設備の生産性維持・向上が保全活動の目的といえます。
たとえば設備の突発的な故障や事故は製造現場の生産性を著しく低下させ、生産計画に大きな影響を及ぼします。 それを防止するための日常点検や保守の重要性は言うまでもありませんが、さらに一歩進めて、“設備の5S”や“全社を巻き込んだ保全活動の大切さ”について前回はお話ししました。 特に製造現場で多発するチョコ停の対策には、設備部門と製造ラインの協働が必要不可欠です。
そこで今回は、“チョコ停の防止”を中心とした設備保全活動を考えたいと思います。
設備保全は4つに分類される
チョコ停の対策を考えるにあたって、保全活動は4つに分類できます。
それをまとめると以下のようになります。
1)事後保全:故障や停止、有害な機能低下が発生してから修理する保全方法。
2)予防保全:日常点検による劣化防止、一定周期での定期点検、オーバーホールなどの方法。
3)改良保全:同じ故障が発生しないように改善を加える方法。
4)保全予防:設備の計画段階から保全を考えていく方法。
1)事後保全は、緊急時や突破的な故障に対応する方法です。仮に故障しても代替機がある場合は事後保全も可能ですが、予防やコストの概念に乏しく成り行き任せの感があります。
2)予防保全は、メンテナンスや定期点検による保全、オーバーホールなどを指します。たとえば自動車などは、6か月、12月点検など時間基準で保全が行われています。
3)改良保全は、再発防止のため頑丈な部品と交換するなど、設備の弱点を補強する方法です。
4)保全予防とは、工場設計や新しい機械設備を設置する時点での保全であり、最初の段階で信頼性を追究することにより、初期コストがかかっても長期的にはプラスの効果を求めるものです。
このように設備保全には、その目的や手法に違いがあります。しかし、重要なことは設備部門の仕事の基準を決め、全社を設備保全活動に巻き込むことです。
チョコ停の防止に関しては、予防保全を中心として改良保全が必要になる場合もありますが、本当の意味で大切なことは保全予防の段階で設備のスペックを最大限引き出すことです。
チョコ停はなぜ発生するのか
設備の寿命はバスタブ曲線で表されます(図1)。
新しい設備の導入後は高い発生率で故障が起こります。これを初期故障期といいます。実はこのタイミングでチョコ停を撲滅しなければ、その後、慢性的なチョコ停が発生するようになります。
機械のクセや調整で取り残された部分が不具合として残っているのです。また設備に常にかかり続ける負荷、つまり設備内で発生する機械的・電気的ストレスや、外部要因としての温度・湿度・振動・粉塵などが影響を及ぼしています。その累積が慢性的なチョコ停の原因となっているわけです。 故障の原因はいくつもありますが、メンテナンス不足でフル稼働を続ける状況では、時間と共に劣化が進行することは目に見えています。設備の補修・管理を組み込んだ生産計画の見直しが重要です。 また、操作ミスや間違った使用条件を繰り返すことで劣化を招くこともあります。修理において、壊れやすいと考えていた部分以外に故障や劣化の要因があったり、許容量を超えた条件で使用されていた場合などです。 また部品の強度不足、設計・施工上の技術的問題などもチョコ停の原因となります。
チョコ停の現象は様々です。いろいろな対策を講じても再発し、繰り返し類似のトラブルが発生するため根負けしあきらめている場合も多いようです。
チョコ停が一番多く発生するのは、加工・組立の自動機の場合で、手作業を安易にロボット化して自動組立に合った部品形状などを考えずに実施した場合などに見受けられます。
また、搬送・位置決め・取出しや取付け・反転・ワーク確認などでもよく発生しています。
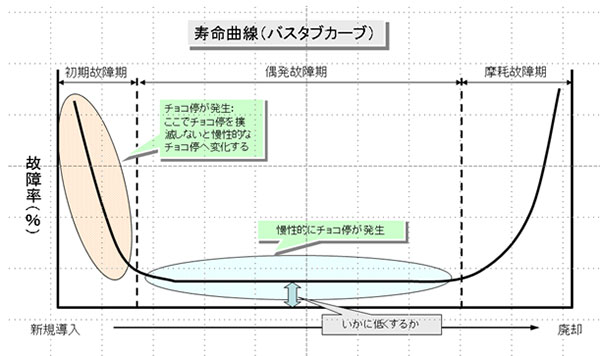
寿命曲線(バスタブカーブ)
製造部門と設備部門のコミュニケーションが重要
チョコ停対策には、清掃、給油、増締めなどの日常メンテナンスを通じて設備の状態をつかむことが必要です。現場の作業者だからこそ、いつも緩む場所があるということに気づきます。 また現場の仕事である日常点検表などの保全データを分析して対策を検討することも大切です。
簡単な部品交換や応急処置も保全部門に任せた上に、故障や不具合の連絡も遅く、不明確な状況では緊急の事故発生時には対応できません。老朽化が進んでいくと点検サイクルも変わってくるのですが、応急処置に終始していては再発を繰り返すだけです。
特に設備稼働が安定する偶発故障期のチョコ停発生率を低くするには早期の対策が重要です。
故障発生の頻度により、1年に1回なら予防保全などを決めておく。 先ほどお話ししたように、生産が始まってから設備を改善するのは難しい部分が多く、チョコ停の根本的な部分を直していこうとすれば改良保全となるわけですが、最初にどこまで問題が解決できているかが重要なのです。
設備保全は、チョコ停の多い対策を順番にやっていけばよいと思います。 そして、その根底に出てくるのは先程から何度もお話したように、設備保全部門だけでなく「製造現場を含めた全社の巻き込み」ということです。 設備保全部門の味方を増やしていく。製造のなかで設備に強い人材を育てていく。それが設備保全にとって何よりも大切な事なのです。
以上