Consulting business
Practical consulting
For 40 years, the Techno Management Research Institute (TMRI) has been helping manufacturing sites innovate their management practices by providing results-driven “practical consulting” services tailored to the manufacturing industry. Through our work, we guide businesses towards innovation by showing them how to change the way their people think and act using VPM ® (Value Producing Management) -- an original approach to management that focusses on activating human resources in order to spawn productivity increases and new value creation from the frontline of work. Business continue to learn how to apply VPM ® to solving problems not just on their production floors but also in each of their business processes from development and design to procurement, logistics and sales.
Consulting policy
- Choose improvement themes that can produce concrete results in a short amount of time.
- Promise and deliver big results.
- Emphasize human resource development that translates into improvements in corporate profitability and business activity.
- Provide practical guidance on getting the facts first-hand.
- Improve performance by changing how personnel think and act in ways that cause positive changes at the frontline of business.
- Make the client glad that they sought help from TMRI.
What we mean by “practical consulting”
6 areas of consulting
TMRI categorizes its consulting themes into the 6 areas of “Manufacturing”, “Human resources”, “Plants and equipment”, “International business development”, “Indirect processes” and “Other”. We have and can of course provide consulting services on many other themes.
Manufacturing
- • Productivity improvement of manufacturing sites
- • Defect reduction, yield and quality improvements
- • Shortening of lead time and inventory reduction
Human resources
- • Skill transmission
- • Improvements in corporate climate
- • Awareness enhancement
- • Improvements in motivation
- • Employee training
Plants and equipment
- • Improvements in plants and equipment
- • Improvements in layout
- • Energy and resource conservation
- • New factory starts
Overseas business development
- • Support for overseas factory starts
- • Productivity improvements of overseas factories
- • Training for locally hired human resources
Other
- • New business launches
- • Sales force capacity and channel building
- • IT strategies and web marketing
- • Acquisition of ISO certification
Indirect processes
- • Support for workstyle reform
- • Productivity improvement in back-office operations
- • Cost reduction in procurement
- • Improvements in development management
- • Design innovation and accelerationv
How our original VPM ® approach works
- Discover untapped strengths in personnel
- Trust their potential
- And assign them new value (responsibility)
- By looking at them in a new light
- Understanding the difficulties of their job
- And eliminating wasteful work
- From within their valuable time.
- A worker once candidly asked, “How do I know if I’m wasteful?”
Our response was to “Look for value first and then decide.” - VPM ® (Value Producing Management) is an original approach to managing a business formulated by the Techno Management Research Institute. Using VPM ®, a business identifies waste of all sorts and then changes the way its personnel think and act to eliminate that waste and improve its corporate value. Innovating business by changing the way people think and act is the underlying concept of the practical consulting services that TMRI offers.
VPM ® works because it focusses on activating a business’s human resources. After applying it, productivity increases and new value creation become driven by a reshaped and motivated workforce. Moreover, VPM ® is effective at solving problems not just on production floors but also in each of the business processes from development and design to procurement, logistics and sales.
3 steps to innovating a factory using VPM ®
VPM ® uses a 3-step process to innovate factories.
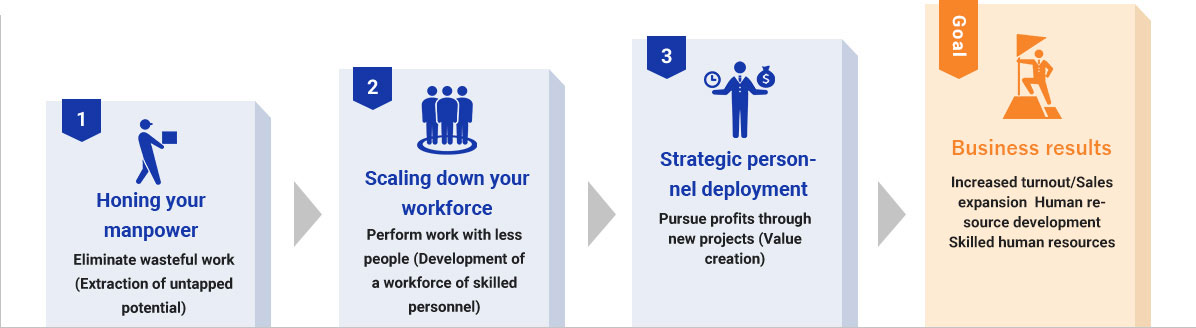
-
Step
Honing your manpower
Eliminate wasteful work (Extraction of untapped potential)The purpose of honing your manpower is to gain greater value by reducing work that does not bear value. In this step, you determine what qualifies as “value” and what constitutes “waste” in your work and thoroughly eliminate that waste.
-
Step
Scaling down your workforce
Perform work with less people (Development of a workforce of skilled personnel)Scaling down your workforce means to free up untapped potential by making it possible to perform work with less people than you currently deploy. Even if you reduce waste by honing your manpower, it will not change your bottom-line unless those improvements are coupled with a reduction in the number of deployed personnel. Therefore, this step is about changing how work is performed by prioritizing the development of a workforce of skilled personnel.
-
Step
Strategic personnel deployment
Pursue profits through new projects (Value creation)The idea behind strategic personnel deployment is to strategically use human resources to build new revenue streams. Business innovation does not end with a scaled down workforce of skilled personnel that masterfully perform their jobs. That’s great, but continuous business growth comes from constructively reinvesting the human resources those efforts freed up as untapped potential in future revenue sources such as “increased turnout”, “sales expansion” or “human resource development”. Before reading on, understand that strategic personnel deployment means to take capable human resources from their current jobs and put them in new positions that add to business. It does not mean to outcast incapable personnel.
Strategic personnel deployment leads to continued corporate growth by investing capable human resources into finding and building new sources of revenue.
Overseas factory diagnoses
- Visualization of physical and information wastes, inconsistencies and stresses
TMRI solves the problems that give business leaders and factory managers headaches - Understanding the present situation is the starting point for changing the future. TMRI not only analyzes an organization for its strengths and weaknesses and identifies trouble areas but also proposes ways for it to realize the “improved profitability”, “human resource development” and other goals set forth in its corporate vision.
Open seminars
TMRI organizes open seminars on the latest themes. We have a vast library of business knowledge to draw from for this purpose and have amassed an impressive track record of staged events and programs not only in Japan but overseas as well in places like East Asia and Southeast Asia. Our local subsidiary in Thailand, TMCT, periodically holds seminars, as well.
-
Management innovation seminars
Management innovation is a subject that interests business leaders, so TMRI periodically holds seminars on related topics for upper and midlevel management in all parts of the country. Consultants from the frontline in each region speak at these seminars, so they are familiar with the local business landscape and, because of their daily consulting jobs, can convincingly explain how to go about innovating management.List of seminars( Japanese site) -
Technology seminars
Our technology seminars are open events for business communities that are seeking to build up the technological and skill foundations needed for manufacturing or improvement activities. Because we have our own seasoned consultants speak at these seminars, the content is specific and to the point. These seminars are highly recommended for persons interested in learning a “step-by-step approach to innovation/improvement” and applying it to their business processes.
List of seminars( Japanese site)
Internal workshops (Conducted at the client’s business site by consultants sent from TMRI)
- Curriculums customized to request
- These workshops are for midlevel managers and personnel, and are conducted at the client’s place of business by highly experienced instructors dispatched from TMRI. Curriculums can also be customized to the hosting business. In contrast to the generalized topics of our open seminars, these workshops are based on actual workplace problems, therefore participants not only acquire knowledge but also discover hints on how to improve actual business processes.
Consulting on overseas business development
From Japan to Asia and others parts of the world